Saturday, June 23, 2007
lowering the underhood temps
http://www.oldspower.com/vb/showthread.php?t=6068
Q: What is the difference in ceramic coated headers and "normal" headers? Are the ceramic ones worth the extra dough?
A: Basically a ceramic coated header has a coating on it that keeps it looking good and reduces engine bay temps down whereas a regular header just has paint on it which will all be gone within 10 minutes of running time and the engine compartment temp will soar. If you can part with the dough, ceramic coating is a very good idea. Magazines that do dyno tests have also seen hp gains from ceramic coating too.
The reason for the HP gains is that the ceramic coating is an excellent heat insulator and keeps the exhaust gases inside the pipes hot. The hot gases have more kinetic energy and will therefore move through the system faster, which enhances the exhasut flow and the scavenging effect in the cylinders.
Keeping the pipes looking nice and lowering the underhood temps are an added bonus!
I was thinking - you could buy regular headers, "custom" fit them to your car (you know, with hammer dents in the appropriate places) and then send them to Jet Hot or whoever and have them ceramic coated. Then they'll fit perfectly and you won't have to worry about damaging the coating when installing them.
Q: What is the difference in ceramic coated headers and "normal" headers? Are the ceramic ones worth the extra dough?
A: Basically a ceramic coated header has a coating on it that keeps it looking good and reduces engine bay temps down whereas a regular header just has paint on it which will all be gone within 10 minutes of running time and the engine compartment temp will soar. If you can part with the dough, ceramic coating is a very good idea. Magazines that do dyno tests have also seen hp gains from ceramic coating too.
The reason for the HP gains is that the ceramic coating is an excellent heat insulator and keeps the exhaust gases inside the pipes hot. The hot gases have more kinetic energy and will therefore move through the system faster, which enhances the exhasut flow and the scavenging effect in the cylinders.
Keeping the pipes looking nice and lowering the underhood temps are an added bonus!
I was thinking - you could buy regular headers, "custom" fit them to your car (you know, with hammer dents in the appropriate places) and then send them to Jet Hot or whoever and have them ceramic coated. Then they'll fit perfectly and you won't have to worry about damaging the coating when installing them.
How can I ceramic coat the inside of my headers?
I've been told that the spray on ceramic coating Satin Black sold by Techline can be applied to the interior of the headers.
I tried and after a few minutes the ceramic material I has applied to the interior came out the end of the headers.
The exterior coating is still on and holding well.
Thanks
I tried and after a few minutes the ceramic material I has applied to the interior came out the end of the headers.
The exterior coating is still on and holding well.
Thanks
Doing it the hard way ..... and how!
http://www.classicalpontiac.com/restoration/4.html
For those of you who may be on a budget and still want to have longer lasting and non-rusting headers. You may want to try and coat them yourself. I had planned on the old BBQ black paint again. Then I came across a product called CERMAKROME made by TechLine. Its a high temp thermal barrier metallic/ceramic coating. IÕm sure there are other coatings on the market. I just happened to use this particular one.
In order to coat the headers properly you will need access to the following equipment and supplies:
a. sand blaster
b. airbrush or touchup sprayer
c. oven/heat source
d. 6 aluminum oven liners approx. 16"x18"(from supermarket)
e. fiber glass house insulation
The coating instructions are: sand blast the headers. Make sure all paint, rust and oils are 100 percent off. Do not bead blast. It doesn't open the metal surface like sand does or removes rust completely. Wipe parts with alcohol thinner or acetone. Do not use petroleum-based products. Warm parts to approximately 90 degrees. I used my wood stove in the garage. A heat gun would work also. This is to make sure no moisture is in the metal. The instructions say to spray a light fog on the radius first, then the rest of the pipe. I found that this left dry spots that when the over spray from spraying the rest of the pipe, left a bumpy, orange peel like texture. I found that by painting like I normally paint a part it work better. I kept a wetness to all of the area I was working on then moved down the pipe. Which kept the coating smooth looking and the finished results were far better.
But remember not to get it to thick.
I used an airbrush. I think a touchup gun may be too large to use. At least for me. Seeing that the pipes were pre-heated the coating starts to dry quickly. I hung the pipes from a wire so I could get 360 degrees around them. This let me start at the top and work my way down and around. I did spray the hard to get to areas first, of the section I was working on. Like where the pipe tubes come together as a group. Continue until the header is totally coated. The coating should be a .001" to .0015" thick. I couldn't mike it so I just put on a medium paint type thickness. The coating is now a light green color. The part now needs to be heated to about 150 degrees in an oven to dry. (10 min) The dry coating is a light gray. Then the part needs to be baked at 500 degrees for one hour. No you don't have to baste.
I used the household oven. Here's how. Seeing the oven door wouldn't close with the pipe in there. I extended the oven door. I put the pipe in the stove from rear corner to the opposite front corner. I wired the front corner to hang up to the top of the open end of the oven. I closed the door as far a possible. This will leave a tri-angle shape for the sides and a longer rectangle opening on top. I then cut and formed the oven pans to the tri-angles and made them about 1 _" thick. I stuffed them with the insulation. I did the same for the top opening. The oven pans are like aluminum pie pans, very easy to bend. This was also wrapped with aluminum foil to help seal on the oven and door areas. Of coarse you want to have this done prior to painting the pipe. Make sure that any oven switches (light inside) get insulated from the heat or they kinda melt. Make sure they have foil around them and are exposed to the outside of the stove if you can. I put an oven pan on the floor of the oven just in case.
There were no toxic type fumes or smells. Yes there was a baked surface smell but it wasn't that strong. I would try to close off the kitchen and open a window. After baking at 500 degrees for an hour let cool, do not quench. There will be a light gray /dirty white color on the pipe. Now take some "00" steel wool or medium scotch brite pads and start to sand the surface. What will appear will be a metallic coating. Which looks a lot like the "Jet Coatings", that you pay big $$s for, on the outside of your pipes. If you had a car undercoating type spray wand I'm sure you could also paint the inside. This is very similar to powder coating because the coating is made up of aluminum powder and phosphate/chromic solution. You then can keep sanding until they are polished or close to it.
There are several aspects I like about this type of coating. You can coat just about anything that can withstand 500 degrees (not internal engine parts). Also to touch up a nick in the coating, for headers, is warm engine, touch up then drive. This coating is very tuff but will scratch or chip if hit hard enough with some thing hard. Like a wrench when tightening the header bolts. The coating has been tested to a continuous 1200 degrees. It won't turn color and keeps the heat inside the pipe vs. the engine compartment. It can be cleaned up and thinned with water. Unless it dries first, so be careful about spillage.
For those of you who may be on a budget and still want to have longer lasting and non-rusting headers. You may want to try and coat them yourself. I had planned on the old BBQ black paint again. Then I came across a product called CERMAKROME made by TechLine. Its a high temp thermal barrier metallic/ceramic coating. IÕm sure there are other coatings on the market. I just happened to use this particular one.
In order to coat the headers properly you will need access to the following equipment and supplies:
a. sand blaster
b. airbrush or touchup sprayer
c. oven/heat source
d. 6 aluminum oven liners approx. 16"x18"(from supermarket)
e. fiber glass house insulation
The coating instructions are: sand blast the headers. Make sure all paint, rust and oils are 100 percent off. Do not bead blast. It doesn't open the metal surface like sand does or removes rust completely. Wipe parts with alcohol thinner or acetone. Do not use petroleum-based products. Warm parts to approximately 90 degrees. I used my wood stove in the garage. A heat gun would work also. This is to make sure no moisture is in the metal. The instructions say to spray a light fog on the radius first, then the rest of the pipe. I found that this left dry spots that when the over spray from spraying the rest of the pipe, left a bumpy, orange peel like texture. I found that by painting like I normally paint a part it work better. I kept a wetness to all of the area I was working on then moved down the pipe. Which kept the coating smooth looking and the finished results were far better.
But remember not to get it to thick.
I used an airbrush. I think a touchup gun may be too large to use. At least for me. Seeing that the pipes were pre-heated the coating starts to dry quickly. I hung the pipes from a wire so I could get 360 degrees around them. This let me start at the top and work my way down and around. I did spray the hard to get to areas first, of the section I was working on. Like where the pipe tubes come together as a group. Continue until the header is totally coated. The coating should be a .001" to .0015" thick. I couldn't mike it so I just put on a medium paint type thickness. The coating is now a light green color. The part now needs to be heated to about 150 degrees in an oven to dry. (10 min) The dry coating is a light gray. Then the part needs to be baked at 500 degrees for one hour. No you don't have to baste.
I used the household oven. Here's how. Seeing the oven door wouldn't close with the pipe in there. I extended the oven door. I put the pipe in the stove from rear corner to the opposite front corner. I wired the front corner to hang up to the top of the open end of the oven. I closed the door as far a possible. This will leave a tri-angle shape for the sides and a longer rectangle opening on top. I then cut and formed the oven pans to the tri-angles and made them about 1 _" thick. I stuffed them with the insulation. I did the same for the top opening. The oven pans are like aluminum pie pans, very easy to bend. This was also wrapped with aluminum foil to help seal on the oven and door areas. Of coarse you want to have this done prior to painting the pipe. Make sure that any oven switches (light inside) get insulated from the heat or they kinda melt. Make sure they have foil around them and are exposed to the outside of the stove if you can. I put an oven pan on the floor of the oven just in case.
There were no toxic type fumes or smells. Yes there was a baked surface smell but it wasn't that strong. I would try to close off the kitchen and open a window. After baking at 500 degrees for an hour let cool, do not quench. There will be a light gray /dirty white color on the pipe. Now take some "00" steel wool or medium scotch brite pads and start to sand the surface. What will appear will be a metallic coating. Which looks a lot like the "Jet Coatings", that you pay big $$s for, on the outside of your pipes. If you had a car undercoating type spray wand I'm sure you could also paint the inside. This is very similar to powder coating because the coating is made up of aluminum powder and phosphate/chromic solution. You then can keep sanding until they are polished or close to it.
There are several aspects I like about this type of coating. You can coat just about anything that can withstand 500 degrees (not internal engine parts). Also to touch up a nick in the coating, for headers, is warm engine, touch up then drive. This coating is very tuff but will scratch or chip if hit hard enough with some thing hard. Like a wrench when tightening the header bolts. The coating has been tested to a continuous 1200 degrees. It won't turn color and keeps the heat inside the pipe vs. the engine compartment. It can be cleaned up and thinned with water. Unless it dries first, so be careful about spillage.
Porsche ceramic exhaust
http://brentwoodrocketscience.com/r2/r2.htm
I acquired a 3.2 liter engine last year for the RSR project which was ulitmately sold as a rolling chassis. After some difficulty trying to sell the 3.2 longblock, it hit me one day...Why not build it and use it. After all, my 72' 911 chassis is pre-emissions so all the stops could be pulled out for a little hotter engine.
So, through word of mouth the 2.7 built almost 2 years (and 3,000 miles) ago is finding a home in a nicely done 914-6.
Nice mention of ceramic exhaust on Porsche.
I acquired a 3.2 liter engine last year for the RSR project which was ulitmately sold as a rolling chassis. After some difficulty trying to sell the 3.2 longblock, it hit me one day...Why not build it and use it. After all, my 72' 911 chassis is pre-emissions so all the stops could be pulled out for a little hotter engine.
So, through word of mouth the 2.7 built almost 2 years (and 3,000 miles) ago is finding a home in a nicely done 914-6.
Nice mention of ceramic exhaust on Porsche.
Pictures and albums about Ceramic headers published in rides
http://www.webshots.com/explains/rides/ceramic-headers.html
Interesting write up here.
New Extractors [Headers for the boys in the USA]published by camsvette in corvettes on 2005-01-03 last update on 2005-06-11The extractors had to be custome made with the fitting of the new Rack And Pinion Steering. All pipes will be ceramic coated when finishedKeywords: corvette, headers, corvette exhaust, headers, ceramic headers, ceramic exhaust
Interesting write up here.
New Extractors [Headers for the boys in the USA]published by camsvette in corvettes on 2005-01-03 last update on 2005-06-11The extractors had to be custome made with the fitting of the new Rack And Pinion Steering. All pipes will be ceramic coated when finishedKeywords: corvette, headers, corvette exhaust, headers, ceramic headers, ceramic exhaust
Johannesburg - June 2005
CBC2 Powerkote Coats Polo Components for Engen VW Cup
Johannesburg - June 2005 - CBC2 Powerkote has successfully applied its high temperature microfilm ceramic coatings to the exhaust manifolds of the 35 cars participating in the Engen VW Cup, part of the national SA Championship Power Tour.
The racing cars were experiencing several heat related problems during the race. Ian Pepper, a driver in the series, commented, "Our vehicles were excessively hot under the bonnet. The oil was running thin; the brake fluid tended to boil during the race, and the clutch fluid disappeared."
"We approached Powerkote to assist us to find a solution to these overheating problems, as well as to reduce the high temperature in the passenger compartments."
Powerkote applied its high temperature thermal barrier coating to all the exhaust manifolds of the 35 vehicles, which not only corrosion-protected the parts, but retained the heat within the manifold or header. This resulted in performance benefits as the exhaust gas velocity was accelerated, which reduced both back pressure and fuel contamination due to reversion.
The surface temperature of the manifold was also reduced substantially, which resulted in minimising the overall heat generated to the passenger compartment, as well as surrounding parts, such as alternators and starters. A secondary benefit was the reduction of heat drawn in through the carburettor.
Pepper added, "The ceramic coating reduced the heat up to 50%, which allowed the vehicles to run more consistently at optimum temperatures, which improved our overall performance."
The Engen VW Cup, which has been running for 9 years, is a popular series as all vehicles have identical specifications which keeps the development costs affordable, and ensures that the playing fields are level, so that the focus is on the drivers' skills.
Powerkote Cape recently sponsored Powerflow's VW Polo by coating the exhaust manifold, pistons and intake manifold for the race in the regional GTi challenge in the Western Cape.
Vehicle owner, Dick Bate, said, "The coating decreased the operating temperature of the engine, particularly the intake manifold, resulting in colder air and more consistent power, which is critical for racing conditions.
Johannesburg - June 2005 - CBC2 Powerkote has successfully applied its high temperature microfilm ceramic coatings to the exhaust manifolds of the 35 cars participating in the Engen VW Cup, part of the national SA Championship Power Tour.
The racing cars were experiencing several heat related problems during the race. Ian Pepper, a driver in the series, commented, "Our vehicles were excessively hot under the bonnet. The oil was running thin; the brake fluid tended to boil during the race, and the clutch fluid disappeared."
"We approached Powerkote to assist us to find a solution to these overheating problems, as well as to reduce the high temperature in the passenger compartments."
Powerkote applied its high temperature thermal barrier coating to all the exhaust manifolds of the 35 vehicles, which not only corrosion-protected the parts, but retained the heat within the manifold or header. This resulted in performance benefits as the exhaust gas velocity was accelerated, which reduced both back pressure and fuel contamination due to reversion.
The surface temperature of the manifold was also reduced substantially, which resulted in minimising the overall heat generated to the passenger compartment, as well as surrounding parts, such as alternators and starters. A secondary benefit was the reduction of heat drawn in through the carburettor.
Pepper added, "The ceramic coating reduced the heat up to 50%, which allowed the vehicles to run more consistently at optimum temperatures, which improved our overall performance."
The Engen VW Cup, which has been running for 9 years, is a popular series as all vehicles have identical specifications which keeps the development costs affordable, and ensures that the playing fields are level, so that the focus is on the drivers' skills.
Powerkote Cape recently sponsored Powerflow's VW Polo by coating the exhaust manifold, pistons and intake manifold for the race in the regional GTi challenge in the Western Cape.
Vehicle owner, Dick Bate, said, "The coating decreased the operating temperature of the engine, particularly the intake manifold, resulting in colder air and more consistent power, which is critical for racing conditions.
Black Satin Results
BHK Results
The following comes from
Chuck McClellan, Orlando, Fl.
So far, I have coated my down pipe and test pipe on my '87 Grand National with the Black Satin. The down pipe temps average 1500-1700 degrees. I recently went to the local drag way and couldn't believe the difference in my engine bay temps compared to other Grand Nationals after each run. My car seemed to cool down quicker and run cooler than before. Everyone thought the BHK would peel off as soon as the DP (Down Pipe) got warm but I have put over 100 miles on the car and its still looks great. I have several local club members wanting to get their DPs and headers coated after seeing mine.
As Dave indicates Black Satin works extremely well.
The following comes from
Chuck McClellan, Orlando, Fl.
So far, I have coated my down pipe and test pipe on my '87 Grand National with the Black Satin. The down pipe temps average 1500-1700 degrees. I recently went to the local drag way and couldn't believe the difference in my engine bay temps compared to other Grand Nationals after each run. My car seemed to cool down quicker and run cooler than before. Everyone thought the BHK would peel off as soon as the DP (Down Pipe) got warm but I have put over 100 miles on the car and its still looks great. I have several local club members wanting to get their DPs and headers coated after seeing mine.
As Dave indicates Black Satin works extremely well.
Performance Report
Performance Report
The following information was provided by Ron, of Accessories Plus.
A diesel truck running a Cummins diesel engine, originally dyno'd at 513 H.P. to the rear wheels. After coating the exhaust manifold, the pipes and the elbows leading to the stacks, but not the mufflers, the truck dyno'd at 524 H.P. at the rear wheels. The driver reported it was quieter and both engine and cab temperatures were cooler.
The following information was provided by Ron, of Accessories Plus.
A diesel truck running a Cummins diesel engine, originally dyno'd at 513 H.P. to the rear wheels. After coating the exhaust manifold, the pipes and the elbows leading to the stacks, but not the mufflers, the truck dyno'd at 524 H.P. at the rear wheels. The driver reported it was quieter and both engine and cab temperatures were cooler.
TEST REPORT
We just received a report on an independent test performed using
CBC2. BCD Coatings of Pulaski, TN, brought this information to our
attention.
The test engine was a Briggs and Stratton. The engine was initially
set up to run tests to determine the effectiveness of different weights
and volume of oil in the engine. The test also included the results
obtained by using an oil additive. A final series of tests were run
using CBC2 on the piston top and the head. The results are found below;
Average HP
Head Temp
Oil Temp
Uncoated
5.86
454f
206f
Coated
6.54
391f
168f
This clearly demonstrates the benefits to be found using CBC2.Over 10%
increase in HP
PLASMA VS LIQUID COATINGS
PLASMA VS LIQUID COATINGS
Several companies offer to apply plasma or flame sprayed coatings to exhaust systems. Typically these will be some form of a Zirconia Ceramic, though they can be metallic as well. The claim is made that these are superior to “other” liquid types of coatings. The “Other” types are generally referred to as primarily being cosmetic. Is this true?When compared thickness for thicknes, no significant difference is observed. When compared by the cost, liquid coatings are much more affordable. In one current AD, by a well known Coating Company who promotes Plasma Sprayed coatings, the AD refers to a 3% to 5% gain in power. Significantly this is in line with our experience with the liquid type coatings we manufacture. In reality H.P. gains will vary considerably depending on a variety of factors. Keeping heat in will accelerate exhaust gas velocity and improve engine efficiency and power. In addition reduced under hood temperatures can increase H.P., by reducing the temperature of the intake charge. Gains of as much as 25 H.P. have been seen.
When you factor in the lower cost, better looks and the proximity of shops applying Tech Line products, it makes good sense to make use of the advanced liquid coating technology available. Not to mention the cost savings available from the coatings we sell that can be applied by the average enthusiast at home.
It should also be considered that for increases in thermal barrier efficiency two basic approaches exist. One is to simply apply a thicker coating. This not only increases cost but weight as well. By using two different liquid coatings, comparable gains can be made, while using a thinner overall coating. This occurs because heat has a tendency to slow when passing through dissimilar materials. An example will be a base coat of HHBK followed by a top coat of BHK. This is more efficient than a comparable coating thickness of just a single material.
An example of the efficiency of our coatings is seen in an independent test run by Competition Cams. They coated one header only on a BB Chevy. The coated side and the uncoated side were both instrumented. The surface temperatures were reduced approximately 300f and in fact the comment made by the technicians was, that just after a dyno pull you could grab the coated header with your hand and not get burned. The radiated heat measured 1 inch away from the coated header was a maximum of 80F and the uncoated side showed 200F. Exhaust gas temperatures were over 1500F.
Good Looks, Efficiency, Cost Savings and Less Weight. Sound good?
Several companies offer to apply plasma or flame sprayed coatings to exhaust systems. Typically these will be some form of a Zirconia Ceramic, though they can be metallic as well. The claim is made that these are superior to “other” liquid types of coatings. The “Other” types are generally referred to as primarily being cosmetic. Is this true?When compared thickness for thicknes, no significant difference is observed. When compared by the cost, liquid coatings are much more affordable. In one current AD, by a well known Coating Company who promotes Plasma Sprayed coatings, the AD refers to a 3% to 5% gain in power. Significantly this is in line with our experience with the liquid type coatings we manufacture. In reality H.P. gains will vary considerably depending on a variety of factors. Keeping heat in will accelerate exhaust gas velocity and improve engine efficiency and power. In addition reduced under hood temperatures can increase H.P., by reducing the temperature of the intake charge. Gains of as much as 25 H.P. have been seen.
When you factor in the lower cost, better looks and the proximity of shops applying Tech Line products, it makes good sense to make use of the advanced liquid coating technology available. Not to mention the cost savings available from the coatings we sell that can be applied by the average enthusiast at home.
It should also be considered that for increases in thermal barrier efficiency two basic approaches exist. One is to simply apply a thicker coating. This not only increases cost but weight as well. By using two different liquid coatings, comparable gains can be made, while using a thinner overall coating. This occurs because heat has a tendency to slow when passing through dissimilar materials. An example will be a base coat of HHBK followed by a top coat of BHK. This is more efficient than a comparable coating thickness of just a single material.
An example of the efficiency of our coatings is seen in an independent test run by Competition Cams. They coated one header only on a BB Chevy. The coated side and the uncoated side were both instrumented. The surface temperatures were reduced approximately 300f and in fact the comment made by the technicians was, that just after a dyno pull you could grab the coated header with your hand and not get burned. The radiated heat measured 1 inch away from the coated header was a maximum of 80F and the uncoated side showed 200F. Exhaust gas temperatures were over 1500F.
Good Looks, Efficiency, Cost Savings and Less Weight. Sound good?
10% increase
Adam of ACR Engines
Adam had his intake coated with our Thermal Barrier and Thermal Dispersant products in an effort to reduce the intake charge temperature, for more power. He measured a 10 H.P. Increase with the coatings.
Adam had his intake coated with our Thermal Barrier and Thermal Dispersant products in an effort to reduce the intake charge temperature, for more power. He measured a 10 H.P. Increase with the coatings.
Corvette Fever
CORVETTE FEVER
In the June issue they had a press release on coated brakes. Two separate references were made to coatings. Both are on page 45. One reference was to the barrier coating and one on the dispersant. Both help keep things cooler. We hope to be able to release the test performed by a major brake manufacturer shortly. The results shocked them. Far better than they even hoped for!
In the June issue they had a press release on coated brakes. Two separate references were made to coatings. Both are on page 45. One reference was to the barrier coating and one on the dispersant. Both help keep things cooler. We hope to be able to release the test performed by a major brake manufacturer shortly. The results shocked them. Far better than they even hoped for!
Precision Engine Magazine
PRECISION ENGINE MAGAZINE
Jan /Feb 2003
More and more attention is being given to the coating of Internal Engine parts. The latest edition of Performance Engine magazine includes an article titled "Performance Engine Bearing Technology". In the article it addresses the benefits of coated bearings. It makes the point that coated bearings are not just for the professional engine builder and pro racers. They state; "it's the weekend race with a limited budget who can benefit ...." It then discusses the benefits when the oil film breaks down, which is a regular occurrence. In addition it draws attention to coatings used to protect the camshaft.
Jan /Feb 2003
More and more attention is being given to the coating of Internal Engine parts. The latest edition of Performance Engine magazine includes an article titled "Performance Engine Bearing Technology". In the article it addresses the benefits of coated bearings. It makes the point that coated bearings are not just for the professional engine builder and pro racers. They state; "it's the weekend race with a limited budget who can benefit ...." It then discusses the benefits when the oil film breaks down, which is a regular occurrence. In addition it draws attention to coatings used to protect the camshaft.
Speedway Illistrated Discussion
Speedway Illustrated Magazine
An article has appeared in this magazine discussing the advantages to be found in using Thermal Barrier Coatings authored by David Vizard. It includes information on the benefits to be found in coating intake manifold bottoms as well as coating the intake runners. By coating these surfaces you can effectively reduce the intake temperature as well as reduce the heat that can be absorbed by the air or air / fuel mix as it passes through the runners.
An additional point was made about the gain that can be seen by coating the intake valve. The incoming air/fuel mixture will pass over the valve just before entering the combustion chamber. When the mix passes over the valve it will pick up heat that has been absorbed by the valve, during combustion. This can lead in extreme cases to detonation. In less extreme cases it still can reduce power. Coating the valve reduces the heat absorbed and contributes to a "cooler" air fuel mix, which means a greater power potential. Wheel Coatings
There is a great deal of interest in wheel coatings. This is of special, interest to Circle Track competitors as wheel and tire temperatures are critical. Tech Line Coatings has been recommending a variety of coatings for wheels. By choosing the proper coating wheel, tire and break temperatures can be controlled to a beneficial degree.
An article has appeared in this magazine discussing the advantages to be found in using Thermal Barrier Coatings authored by David Vizard. It includes information on the benefits to be found in coating intake manifold bottoms as well as coating the intake runners. By coating these surfaces you can effectively reduce the intake temperature as well as reduce the heat that can be absorbed by the air or air / fuel mix as it passes through the runners.
An additional point was made about the gain that can be seen by coating the intake valve. The incoming air/fuel mixture will pass over the valve just before entering the combustion chamber. When the mix passes over the valve it will pick up heat that has been absorbed by the valve, during combustion. This can lead in extreme cases to detonation. In less extreme cases it still can reduce power. Coating the valve reduces the heat absorbed and contributes to a "cooler" air fuel mix, which means a greater power potential. Wheel Coatings
There is a great deal of interest in wheel coatings. This is of special, interest to Circle Track competitors as wheel and tire temperatures are critical. Tech Line Coatings has been recommending a variety of coatings for wheels. By choosing the proper coating wheel, tire and break temperatures can be controlled to a beneficial degree.
Dyno Test
Dyno Test
From Sartor Bros. in South Africa.
A test was performed in South Africa to see to what extent header coatings could reduce the surface temperatures on stock exhaust manifolds . The test was to see if the coatings would allow the vehicles to meet or be exempt from Regulation 10.25.2(b) of the Mine Health and Safety Act of 1996. A Toyota 2 ton truck running a 2L: diesel was to be used. Sartor Bros coated the test engines manifolds with Tech Line coating products.
TIt is necessary to reduce the surface temperatures as there is a significant danger of igniting gases when the equipment is use, in these huge underground mines. The test was conducted at Twistdraai Central Colliery.
The Results were as follows:
The maximum temperature of the manifold( at the exhaust flange) was 166C. ( Previously recorded 238C). This was at the steepest incline of the mine. The highest temperature on level ground was 142C. The highest exhaust branch outlet temperature was 129C.
If you convert to Fahrenheit, the drop was from 460f to 330f. Since the uncoated temperature was high enough to cause ignition of the gases this reduction is significant and would potentially allow the use of these engines in the mines.
CBC2/CBX and Compression Ratios. We are regularly asked how much additional compression can be run when one of Tech Line’s thermal barrier coatings are used on piston tops. Since the coating changes the efficiency of the combustion chamber and reduces the likelihood of entering into detonation, it is possible to run more compression.Since there are so many variables we cannot give an absolute figure. However in general you can run 1 point more in compression. We have had reports over the years that 10.5 to 10.75 is possible. It should be noted that in one instance a 302 Ford engine was built that had 12 to 1 compression and was able to be driven and raced on pump gas. One of our own employees ran a 302 Chevy engine, with a nice street cam with a nominal 12 to 1 compression and he regularly drove it to work on pump gas with no problems.
You can find more information at HTTP://www.engineceramics.com
From Sartor Bros. in South Africa.
A test was performed in South Africa to see to what extent header coatings could reduce the surface temperatures on stock exhaust manifolds . The test was to see if the coatings would allow the vehicles to meet or be exempt from Regulation 10.25.2(b) of the Mine Health and Safety Act of 1996. A Toyota 2 ton truck running a 2L: diesel was to be used. Sartor Bros coated the test engines manifolds with Tech Line coating products.
TIt is necessary to reduce the surface temperatures as there is a significant danger of igniting gases when the equipment is use, in these huge underground mines. The test was conducted at Twistdraai Central Colliery.
The Results were as follows:
The maximum temperature of the manifold( at the exhaust flange) was 166C. ( Previously recorded 238C). This was at the steepest incline of the mine. The highest temperature on level ground was 142C. The highest exhaust branch outlet temperature was 129C.
If you convert to Fahrenheit, the drop was from 460f to 330f. Since the uncoated temperature was high enough to cause ignition of the gases this reduction is significant and would potentially allow the use of these engines in the mines.
CBC2/CBX and Compression Ratios. We are regularly asked how much additional compression can be run when one of Tech Line’s thermal barrier coatings are used on piston tops. Since the coating changes the efficiency of the combustion chamber and reduces the likelihood of entering into detonation, it is possible to run more compression.Since there are so many variables we cannot give an absolute figure. However in general you can run 1 point more in compression. We have had reports over the years that 10.5 to 10.75 is possible. It should be noted that in one instance a 302 Ford engine was built that had 12 to 1 compression and was able to be driven and raced on pump gas. One of our own employees ran a 302 Chevy engine, with a nice street cam with a nominal 12 to 1 compression and he regularly drove it to work on pump gas with no problems.
You can find more information at HTTP://www.engineceramics.com
Friday, June 22, 2007
Coating Valve Springs
Coating Valve Springs
Valve Springs are subject to two types of friction. The first is internal friction that occurs due to the movement of the spring as it flexes. The second is external and is developed as the spring moves against another surface. Even single spring sets develop friction through rubbing against the head/ shim and the retainer. The result of this friction is heat and wear. By far heat is the greatest enemy of steel springs. Steel springs will fatigue if the temperature of the spring reaches 400F. At this point the spring will lose a significant amount of its designed tension and will be essentially useless for performance use. Stainless springs can generally handle temperatures approaching 900F. By applying a properly formulated Dry Film Lubricant, the life of the spring can be enhanced significantly. In testing, valve spring life in Performance Applications has shown increases from 2 to 10 times the norm. How is this accomplished? Primarily through a reduction in the heat generated by friction. This is accomplished through more efficient thermal transfer. In addition, the lubricity of the coating will reduce the heat that is generated by externally induced friction. The heat that is generated can actually cause the spring to break, not just fatigue. This might be likened to the effect of flexing a piece of steel. If repeated flexing is done the metal will eventually break at the point showing the most deflection, which many times are also the thinnest areas. That point will also be very hot to the touch as the internal friction is highest at that point. The amount of heat that is generated by a valve spring in motion will vary over the surface of the spring. When multiple springs are run together in a stack, the frictional created heat is increased.
By coating a spring we reduce the heat that can build up in two ways. The First is through the reduction in externally generated friction. By coating the spring, sliding or rubbing friction is reduced with a measurable reduction in the valve spring temperature. The Second way is very important. A properly formulated coating will also more evenly distribute the heat over the surface of the spring reducing the likelihood of generating a hot spot, leading to breakage. In addition, a properly formulated coating will aid in more rapid transfer of the heat generated to the oil, which cools the spring. Unfortunately, some coating systems actually insulate the spring from the oil which can have a detrimental effect on spring life. The ability of a coating to reduce friction also means it will reduce wear. Since valve springs do not uniformly contact another surface, the wear pattern is not even. As wear occurs, the spring can become weaker in these areas and ultimately break. This is particularly true in multiple spring stacks, but is also seen in single spring application. Considering that in many racing applications, springs will barely survive the race, any increase in the ability of the spring to maintain proper seat pressure is desirable. By combining reduced friction and wear with reduced heat generation and enhanced cooling of the spring, spring life and performance can dramatically increase.
More information can be found at http://www.engineceramics.com
Valve Springs are subject to two types of friction. The first is internal friction that occurs due to the movement of the spring as it flexes. The second is external and is developed as the spring moves against another surface. Even single spring sets develop friction through rubbing against the head/ shim and the retainer. The result of this friction is heat and wear. By far heat is the greatest enemy of steel springs. Steel springs will fatigue if the temperature of the spring reaches 400F. At this point the spring will lose a significant amount of its designed tension and will be essentially useless for performance use. Stainless springs can generally handle temperatures approaching 900F. By applying a properly formulated Dry Film Lubricant, the life of the spring can be enhanced significantly. In testing, valve spring life in Performance Applications has shown increases from 2 to 10 times the norm. How is this accomplished? Primarily through a reduction in the heat generated by friction. This is accomplished through more efficient thermal transfer. In addition, the lubricity of the coating will reduce the heat that is generated by externally induced friction. The heat that is generated can actually cause the spring to break, not just fatigue. This might be likened to the effect of flexing a piece of steel. If repeated flexing is done the metal will eventually break at the point showing the most deflection, which many times are also the thinnest areas. That point will also be very hot to the touch as the internal friction is highest at that point. The amount of heat that is generated by a valve spring in motion will vary over the surface of the spring. When multiple springs are run together in a stack, the frictional created heat is increased.
By coating a spring we reduce the heat that can build up in two ways. The First is through the reduction in externally generated friction. By coating the spring, sliding or rubbing friction is reduced with a measurable reduction in the valve spring temperature. The Second way is very important. A properly formulated coating will also more evenly distribute the heat over the surface of the spring reducing the likelihood of generating a hot spot, leading to breakage. In addition, a properly formulated coating will aid in more rapid transfer of the heat generated to the oil, which cools the spring. Unfortunately, some coating systems actually insulate the spring from the oil which can have a detrimental effect on spring life. The ability of a coating to reduce friction also means it will reduce wear. Since valve springs do not uniformly contact another surface, the wear pattern is not even. As wear occurs, the spring can become weaker in these areas and ultimately break. This is particularly true in multiple spring stacks, but is also seen in single spring application. Considering that in many racing applications, springs will barely survive the race, any increase in the ability of the spring to maintain proper seat pressure is desirable. By combining reduced friction and wear with reduced heat generation and enhanced cooling of the spring, spring life and performance can dramatically increase.
More information can be found at http://www.engineceramics.com
Coating Valve Train Components
Coating Valve Train Components
T he valve train sees many benefits from the use of Dry Film Lubricants. All of the parts are minimally lubricated by engine oil. Consequently, excessive wear is always of concern, especially at start up or after the engine has been sitting for an extended period. By using an Extreme Pressure Bonded Lubricant we can provide protection well beyond that ex pected from even the best motor oils. The primary components to be coated are the Cam, Lifters, Push Rods and Rocker Arms ( Valves will be dealt with seperately ). Normal lub rication is provided by a film of oil that is either pumped to the contact point or is splashed onto the part. In either instance oil film breakdown is of concern. By permanently bonding a lubricating coating in place we enhance the ability of the oil to lubricate and provide add itional lubrication even after the oil film fails. Typical motor oils will fail at pressures below 10,000 psi. Properly formulated bonded lubricants can withstand pressure in excess of 350,000 psi
The Dry Film Lubricant functions in two ways. First, it acts as an "oil retaining material" rather than an oil shedding material, as are some materials like Teflon. This means that it reduces the ability of a small amount of oil to flow rapidly over the coated surface. In doing this it actually reduces friction as the remaining oil slides between the mating surfaces very easily and allows the parts to move much more freely. This action also reduces the like lihood of the oil film being "pushed" off the surface. A secondary benefit to this action is that it allows the oil to absorb more heat, thus helping to cool the parts more effeciently. The enhanced sliding action can be demonstrated by the way a "Slip and Slide" functions. This slick piece of plastic does not allow a body to slide over it until a film of water is pre sent. A small amount of the water is retained by the plastic surface as well as by the skin and clothing of the "slidee". With water running over this slick surface, a body will very easily slide for an extended distance. If the surfaces shed water, the effect wouldn't be as dramatic. The layers of water moving at different speeds act like little "rollers" that allow free movement. The Dry Film Lubricant creates the same effect by retaining a small amount of slower moving oil on the coated surface, thus actually allowing easier movement of the parts.
The Second function takes over when the oil film would normally break down either due to pressure or the effect of high heat on the lubricant and allow metal to metal contact. The bonded coating does not "break down" nor cold flow at higher pressure nor is it significantly affected by high temperatures, thus maintaing a lubricous film between the mating surfaces inhibiting metal to metal contact. This film provides a second layer of protection that normally will lubricate at loads in excess of the "crush" or deformation point of the base metal. This is especially critical at start up when a well defined mating surface is desired and excessive wear due to lack of lubrication can do significant damage. Camshafts especially benefit from the application of a Bonded Lubricant at start up where a cam can be damaged if the lub ricating film is not maintained during break in. The use of a Bonded Lubricant such as CERMA LUBE can in many instances eliminate the need to break in the cam using low pressure valve springs. When we combine these features not only do we see better mating surfaces, we can also expect to see less wear, reduced friction and attendant power gains as well as longer part life. In addition, this can allow the Performance Engine Builder to reduce the amount of oil flow ing to these parts thus directing moore of the oil flow to the crank assmebly. A variety of lub ricating coatings are available for these surfaces. DFL-1, TLML and CERMALUBE are the most popular.
More information can be found at http://www.engineceramics.com/
T he valve train sees many benefits from the use of Dry Film Lubricants. All of the parts are minimally lubricated by engine oil. Consequently, excessive wear is always of concern, especially at start up or after the engine has been sitting for an extended period. By using an Extreme Pressure Bonded Lubricant we can provide protection well beyond that ex pected from even the best motor oils. The primary components to be coated are the Cam, Lifters, Push Rods and Rocker Arms ( Valves will be dealt with seperately ). Normal lub rication is provided by a film of oil that is either pumped to the contact point or is splashed onto the part. In either instance oil film breakdown is of concern. By permanently bonding a lubricating coating in place we enhance the ability of the oil to lubricate and provide add itional lubrication even after the oil film fails. Typical motor oils will fail at pressures below 10,000 psi. Properly formulated bonded lubricants can withstand pressure in excess of 350,000 psi
The Dry Film Lubricant functions in two ways. First, it acts as an "oil retaining material" rather than an oil shedding material, as are some materials like Teflon. This means that it reduces the ability of a small amount of oil to flow rapidly over the coated surface. In doing this it actually reduces friction as the remaining oil slides between the mating surfaces very easily and allows the parts to move much more freely. This action also reduces the like lihood of the oil film being "pushed" off the surface. A secondary benefit to this action is that it allows the oil to absorb more heat, thus helping to cool the parts more effeciently. The enhanced sliding action can be demonstrated by the way a "Slip and Slide" functions. This slick piece of plastic does not allow a body to slide over it until a film of water is pre sent. A small amount of the water is retained by the plastic surface as well as by the skin and clothing of the "slidee". With water running over this slick surface, a body will very easily slide for an extended distance. If the surfaces shed water, the effect wouldn't be as dramatic. The layers of water moving at different speeds act like little "rollers" that allow free movement. The Dry Film Lubricant creates the same effect by retaining a small amount of slower moving oil on the coated surface, thus actually allowing easier movement of the parts.
The Second function takes over when the oil film would normally break down either due to pressure or the effect of high heat on the lubricant and allow metal to metal contact. The bonded coating does not "break down" nor cold flow at higher pressure nor is it significantly affected by high temperatures, thus maintaing a lubricous film between the mating surfaces inhibiting metal to metal contact. This film provides a second layer of protection that normally will lubricate at loads in excess of the "crush" or deformation point of the base metal. This is especially critical at start up when a well defined mating surface is desired and excessive wear due to lack of lubrication can do significant damage. Camshafts especially benefit from the application of a Bonded Lubricant at start up where a cam can be damaged if the lub ricating film is not maintained during break in. The use of a Bonded Lubricant such as CERMA LUBE can in many instances eliminate the need to break in the cam using low pressure valve springs. When we combine these features not only do we see better mating surfaces, we can also expect to see less wear, reduced friction and attendant power gains as well as longer part life. In addition, this can allow the Performance Engine Builder to reduce the amount of oil flow ing to these parts thus directing moore of the oil flow to the crank assmebly. A variety of lub ricating coatings are available for these surfaces. DFL-1, TLML and CERMALUBE are the most popular.
More information can be found at http://www.engineceramics.com/
Coating the Oil Pan
Coating the Oil Pan
To many, the purpose for having an oil pan is simply to keep the oil from running onto the ground. However, the oil pan provides additional functions. It allows the oil to pool at the oil pump pick up and it aids in the cooling of the oil. Many people ask to have their oil pans Teflon coated to aid in oil shedding. While a speedy return of the oil to the sump is desirable, it may not be the best way to go for overall performance. Teflon and similar materials are thermal barriers and would inhibit the pan from cooling the oil.
When coating an oil pan, in most applications, it is important to allow the pan to cool the returning oil. It would be better to use a coating that not only has good oil shedding abilities, but also helps rather than hinders the ability to transfer heat from the hot oil into the pan. In addition, coating the outside of the pan with a thermal dispersant will allow the pan to transfer heat from the metal surface to the surrounding air even faster than bare metal. Painting a pan for appearance, using a typical paint, can reduce the ability of the pan to radiate heat. Chrome plating the pan simply further aggravates the problem. The solution is to use Tech Line's TLTD both inside and out. TLTD is an oil shedding, Thermal Dispersant. In addition, it has excellent corrosion inhibiting characteristics and contains lubricants that reduce the ability of dirt and other debris to accumulate on the outside of the pan. This will allow the oil to return to the sump rapidly and help cool the oil as it runs over the coated surface, as TLTD accelerates the transfer of heat into the pan. The heat now in the pan will also be transfered to the outside air flow faster through the TLTD that has been applied to the exterior of the pan. The result is cooler oil.
TLTD functions in a number of ways. First, by being applied in a very thin coat, it does not significantly reduce the surface area of the pan. Second, it contains thermally active ingredients that carry heat faster than the bare metal of the pan. The lubricants allow the oil to return to the sump faster than over bare metal. The lubricants also reduce the ability of dirt and other debris to stick to the surface. Any build up of debris will reduce the surface area of the pan and reduce its ability to shed heat. Finally, the coating is a very good corrosion inhibitor. The formation of any oxidation layer, either rust on steel or an oxidizing of aluminum, will reduce the ability of the pan to shed heat. When all the characteristics of TLTD are combined, the oil pan functions in the best possible manner. The EXCEPTION to the above would be in the case of an engine used in very short competitive periods such as in the case with Drag Racing. In these instances, an oil shedding thermal barrier such as Tech Line's TLLB should be used. TLLB will allow the oil to return to the sump faster and at the same time keep the oil from cooling by reducing thermal transfer. In Drag Racing and similar activities it is not uncommon for the oil to actually be below the optimum temperate and TLLB will help keep as much heat as possible in the oil while sitting in the staging lanes.
More information can be found at http://www.engineceramics.com/
To many, the purpose for having an oil pan is simply to keep the oil from running onto the ground. However, the oil pan provides additional functions. It allows the oil to pool at the oil pump pick up and it aids in the cooling of the oil. Many people ask to have their oil pans Teflon coated to aid in oil shedding. While a speedy return of the oil to the sump is desirable, it may not be the best way to go for overall performance. Teflon and similar materials are thermal barriers and would inhibit the pan from cooling the oil.
When coating an oil pan, in most applications, it is important to allow the pan to cool the returning oil. It would be better to use a coating that not only has good oil shedding abilities, but also helps rather than hinders the ability to transfer heat from the hot oil into the pan. In addition, coating the outside of the pan with a thermal dispersant will allow the pan to transfer heat from the metal surface to the surrounding air even faster than bare metal. Painting a pan for appearance, using a typical paint, can reduce the ability of the pan to radiate heat. Chrome plating the pan simply further aggravates the problem. The solution is to use Tech Line's TLTD both inside and out. TLTD is an oil shedding, Thermal Dispersant. In addition, it has excellent corrosion inhibiting characteristics and contains lubricants that reduce the ability of dirt and other debris to accumulate on the outside of the pan. This will allow the oil to return to the sump rapidly and help cool the oil as it runs over the coated surface, as TLTD accelerates the transfer of heat into the pan. The heat now in the pan will also be transfered to the outside air flow faster through the TLTD that has been applied to the exterior of the pan. The result is cooler oil.
TLTD functions in a number of ways. First, by being applied in a very thin coat, it does not significantly reduce the surface area of the pan. Second, it contains thermally active ingredients that carry heat faster than the bare metal of the pan. The lubricants allow the oil to return to the sump faster than over bare metal. The lubricants also reduce the ability of dirt and other debris to stick to the surface. Any build up of debris will reduce the surface area of the pan and reduce its ability to shed heat. Finally, the coating is a very good corrosion inhibitor. The formation of any oxidation layer, either rust on steel or an oxidizing of aluminum, will reduce the ability of the pan to shed heat. When all the characteristics of TLTD are combined, the oil pan functions in the best possible manner. The EXCEPTION to the above would be in the case of an engine used in very short competitive periods such as in the case with Drag Racing. In these instances, an oil shedding thermal barrier such as Tech Line's TLLB should be used. TLLB will allow the oil to return to the sump faster and at the same time keep the oil from cooling by reducing thermal transfer. In Drag Racing and similar activities it is not uncommon for the oil to actually be below the optimum temperate and TLLB will help keep as much heat as possible in the oil while sitting in the staging lanes.
More information can be found at http://www.engineceramics.com/
Coating Pistons
Coating Pistons
The piston is one of the very first parts that should be considered for coating. Coating the piston reduces friction and wear, reduces part operating temperature, can increase horse power and torque, reduce or eliminate detonation, allow higher compression ratios to be utilized and allow tighter piston to wall clearances for a better ring seal.
Pistons can be coated with three different systems. They are Dry Film Lubricants, Thermal Barriers and Oil Shedding Coatings. These systems can be beneficial on all pistons whether 4 stroke, 2 stroke, gas, alcohol, diesel, reciprocal or rotary.
We will look at the Thermal Barrier coatings first. Either CBC2 or CBX may be applied. CBX is recommended for all High Compression (13:1 and higher), Turbo Charged, Super Charged or engines running Nitrous Oxide. CBC2 should be run on all other engines. Both CBC2 and CBX insulate the piston against damaging heat transfer, keeping more of the heat generated by combustion, pushing down on the piston for greater power. By retaining minimal heat on the surface of the piston, less heat is transferred to the incoming fuel mixture, leading to a reduction in pre-ignition which leads to detonation. The coatings can also allow heat at the sur face to move more evenly over the surface reducing hot spots and the coatings reflect heat into the chamber for more even distribution of heat, allowing more efficient combustion of the fuel. This allows more of the fuel molecules to be oxidized, which in turn, means less fuel is needed for optimum power. The result is an engine that makes more power, can be run with a leaner air/fuel mix and less initial timing and has less thermal ex pansion due to a reduction in the heat absorbed.
By applying a Dry Film Lubricant, friction, galling and wear is reduced. The lubricants are capable of carrying loads beyond the crush point of the piston. In addition, the lubricants are "fluid retaining" materials that actually hold oil to the surface beyond the pressure where the oil would normally be squeezed off. The ability to carry greater loads, up to 350,000 PSI, while increasing lubricity (reduced friction) allows tighter piston to wall clearances to be run. This leads to better sealing with no increase in friction.
By applying Tech Line's TLTD to the underside of the piston, oil that is splashed onto the piston to cool it will shed rapidly. Heat transfers most rapidly when there is a large difference in temperature. The longer oil clings to a hot surface the hotter the oil becomes. By shedding the cooling oil more rapidly, cooler oil is splashed over the surface more frequently. If the oil "hangs" longer, it absorbes less heat and blocks cooler oil from contacting the hot surface. A cooler piston grows less, allowing tighter piston to wall clearances.
The following are recommended for pistons: DFL-1, TLML, CERMALUBE (Highly recommended), CBC2, CBX and TLTD.
More information can be found at http://www.engineceramics.com/
The piston is one of the very first parts that should be considered for coating. Coating the piston reduces friction and wear, reduces part operating temperature, can increase horse power and torque, reduce or eliminate detonation, allow higher compression ratios to be utilized and allow tighter piston to wall clearances for a better ring seal.
Pistons can be coated with three different systems. They are Dry Film Lubricants, Thermal Barriers and Oil Shedding Coatings. These systems can be beneficial on all pistons whether 4 stroke, 2 stroke, gas, alcohol, diesel, reciprocal or rotary.
We will look at the Thermal Barrier coatings first. Either CBC2 or CBX may be applied. CBX is recommended for all High Compression (13:1 and higher), Turbo Charged, Super Charged or engines running Nitrous Oxide. CBC2 should be run on all other engines. Both CBC2 and CBX insulate the piston against damaging heat transfer, keeping more of the heat generated by combustion, pushing down on the piston for greater power. By retaining minimal heat on the surface of the piston, less heat is transferred to the incoming fuel mixture, leading to a reduction in pre-ignition which leads to detonation. The coatings can also allow heat at the sur face to move more evenly over the surface reducing hot spots and the coatings reflect heat into the chamber for more even distribution of heat, allowing more efficient combustion of the fuel. This allows more of the fuel molecules to be oxidized, which in turn, means less fuel is needed for optimum power. The result is an engine that makes more power, can be run with a leaner air/fuel mix and less initial timing and has less thermal ex pansion due to a reduction in the heat absorbed.
By applying a Dry Film Lubricant, friction, galling and wear is reduced. The lubricants are capable of carrying loads beyond the crush point of the piston. In addition, the lubricants are "fluid retaining" materials that actually hold oil to the surface beyond the pressure where the oil would normally be squeezed off. The ability to carry greater loads, up to 350,000 PSI, while increasing lubricity (reduced friction) allows tighter piston to wall clearances to be run. This leads to better sealing with no increase in friction.
By applying Tech Line's TLTD to the underside of the piston, oil that is splashed onto the piston to cool it will shed rapidly. Heat transfers most rapidly when there is a large difference in temperature. The longer oil clings to a hot surface the hotter the oil becomes. By shedding the cooling oil more rapidly, cooler oil is splashed over the surface more frequently. If the oil "hangs" longer, it absorbes less heat and blocks cooler oil from contacting the hot surface. A cooler piston grows less, allowing tighter piston to wall clearances.
The following are recommended for pistons: DFL-1, TLML, CERMALUBE (Highly recommended), CBC2, CBX and TLTD.
More information can be found at http://www.engineceramics.com/
Coating Cylinder Heads
Coating Cylinder Heads
One of the best applications for coatings is in combustion chamber areas. Coating the combustion chamber of a cylinder head can increase performance significantly. In addition, more compression can be run as the proper coating will provide resistance to detonation. Tuning changes can also increase the level of power generated. Coating the intake and exhaust runners can also impact performance. Coating the exterior and the area under the valve cover can improve heat management. By coating the combustion chamber, we reduce the amount of heat that escapes during the power stroke which means more of the heat generated is utilized in "pushing" the piston down. The coating also insulates the surfaces so that they absorb less heat, reducing the load on the cooling system and reducing the amount of dimensional change the head may see from the heat it absorbs. The coating functions in several ways: (1) To keep heat in (Thermal Barrier) (2) To move heat over the surface to reduce hot spots (Radiation) (3) Reflect heat into "cooler" or shrouded areas of the chamber (Convection) and (4) The coating retains less residual heat from combustion than other thermal barriers, thus transferring less heat to the incoming fuel charge (Reduced Thermal Transfer). Combining these features increases power levels, reduces part operating temperature, aids in reducing detonation and can increase fuel efficiency and reduce emissions. By transferring less heat to the incoming fuel charge detonation is reduced, as pre ignition which causes detonation, is generally the result of excessive heat absorption by the fuel as it enters the combustion chamber. By allowing the heat of combustion to be more efficiently used, the fuel charge is better combusted, allowing more compression while reducing the fuel quantity need (in most cases) and increasing power. By accelerating the burn rate of the fuel, through better heat management, less timing is needed to have the optimum burn occur at top dead center. CBC2 is the standard coating to be used, with CBX recommended for very high compression motors (13:1 and above) or for engines that have tight quench areas as well as Turbo Charged, Super Charged and engines utilizing Nitrous Oxide systems. Coating the ports helps with flow and provides additional thermal benefits. Coating the intake runner with a Dry Film Coating can reduce fuel drop out while insulating the incoming fuel from the heat of the head. Coating the exhaust with TLHB can improve flow by creating a very slick surface, while reducing the amount of heat that can pass from the hot exhaust flow into the head. CBC2 or CBX may also be used in exhaust ports, though they are not as "slick" as TLHB. Coating the exterior of the head with Tech Line's TLTD (Thermal Dispersant) allows for faster transfer of the heat that is absorbed from combustion, into the air flow around the head, thus allowing the head to run cooler. This will impact the amount of heat transferred to the intake manifold as well as reduce the heat that accessories will be exposed to, that are mounted on or near the head. When TLTD is applied to the area under the valve cover, better oil drain back is achieved as well as better thermal transfer to the oil, which is cooling the head and valve springs.
One of the best applications for coatings is in combustion chamber areas. Coating the combustion chamber of a cylinder head can increase performance significantly. In addition, more compression can be run as the proper coating will provide resistance to detonation. Tuning changes can also increase the level of power generated. Coating the intake and exhaust runners can also impact performance. Coating the exterior and the area under the valve cover can improve heat management. By coating the combustion chamber, we reduce the amount of heat that escapes during the power stroke which means more of the heat generated is utilized in "pushing" the piston down. The coating also insulates the surfaces so that they absorb less heat, reducing the load on the cooling system and reducing the amount of dimensional change the head may see from the heat it absorbs. The coating functions in several ways: (1) To keep heat in (Thermal Barrier) (2) To move heat over the surface to reduce hot spots (Radiation) (3) Reflect heat into "cooler" or shrouded areas of the chamber (Convection) and (4) The coating retains less residual heat from combustion than other thermal barriers, thus transferring less heat to the incoming fuel charge (Reduced Thermal Transfer). Combining these features increases power levels, reduces part operating temperature, aids in reducing detonation and can increase fuel efficiency and reduce emissions. By transferring less heat to the incoming fuel charge detonation is reduced, as pre ignition which causes detonation, is generally the result of excessive heat absorption by the fuel as it enters the combustion chamber. By allowing the heat of combustion to be more efficiently used, the fuel charge is better combusted, allowing more compression while reducing the fuel quantity need (in most cases) and increasing power. By accelerating the burn rate of the fuel, through better heat management, less timing is needed to have the optimum burn occur at top dead center. CBC2 is the standard coating to be used, with CBX recommended for very high compression motors (13:1 and above) or for engines that have tight quench areas as well as Turbo Charged, Super Charged and engines utilizing Nitrous Oxide systems. Coating the ports helps with flow and provides additional thermal benefits. Coating the intake runner with a Dry Film Coating can reduce fuel drop out while insulating the incoming fuel from the heat of the head. Coating the exhaust with TLHB can improve flow by creating a very slick surface, while reducing the amount of heat that can pass from the hot exhaust flow into the head. CBC2 or CBX may also be used in exhaust ports, though they are not as "slick" as TLHB. Coating the exterior of the head with Tech Line's TLTD (Thermal Dispersant) allows for faster transfer of the heat that is absorbed from combustion, into the air flow around the head, thus allowing the head to run cooler. This will impact the amount of heat transferred to the intake manifold as well as reduce the heat that accessories will be exposed to, that are mounted on or near the head. When TLTD is applied to the area under the valve cover, better oil drain back is achieved as well as better thermal transfer to the oil, which is cooling the head and valve springs.
Coating Headers and Exhaust Manifolds
Coating Exhaust Manifolds
Exhaust manifolds can either be a cast iron, factory-type manifold or a tube steel header typically used in performance applications, though they are becoming very common in OEM applications. There are a variety of reasons for coating an exhaust manifold header. #1 Corrosion protection. The manifold will live longer as well as look nicer. Whether it is for performance or show, coating an exhaust manifold is valuable to you. #2 The coating is a thermal barrier, thus keeping heat within the manifold or header. There are a number of benefits for this. First, by keeping heat within the manifold, you're going to accelerate the exhaust gas velocity which reduces back pressure and reduces fuel contamination due to reversion. This is a performance benefit. Second, you'll reduce the surface temperature of the manifold. This means if a person comes in contact with it, they are less likely to be burned and leave skin behind. If there is a component close to it, it will not see as much heat as it would with an uncoated manifold. In addition, not as much heat will be radiated under the hood or into the engine compartment. This reduces the underhood temperature which, again, reduces the temperature of surrounding parts, such as, alternators and starters. It also reduces the amount of heat that can be drawn in through the carburetor, which is a secondary performance benefit. There are a variety of coatings that can be used on exhaust manifolds or headers.
The most popular is our Cermakrome. This gives a near-chrome finish, tremendous corrosion protection and is an excellent thermal barrier. On the stock side, our Color-guard Cast Iron is extremely popular, especially with restorers, since it imparts an original, dark cast iron appearance rather than the lighter appearance that is more typical of a bead-blasted finish, which is not truly stock. If someone prefers a lighter appearance, they can mix our Colorguard Cast Iron with our Colorguard Aluminum to arrive at a shade they prefer. Both of these coatings have good thermal stability and are good thermal barriers. We recommend on cast iron, due to it's porosity, that a base coat of Cermakrome be put down first, then bake, then lightly sand blast, then put the color you wish on top. For tube steel headers, you can use our Cermakrome, Colorguard over a base coat, Black Satin, WBX, or WBLX. In most cases a single coating is acceptable. In extreme cases it might be advisable to use a base coat, such as our HHBK with a top coat such as Black Satin or WBX. In addition, you can put down a base coat of the HHBK, top coat it with WBX, and top coat that with our Cerma Clear, creating a glossy black finish that has very good high temperature stability.
We also manufacture an insulating base coat for performance applications where Cermakrome is desired. This is our MCS coating. This can be applied to the outside of the exhaust manifold or header, cured, lightly sand blasted, then a layer of Cermakrome applied over it, cured and polished. This will impart higher temperature capability allowing Cermakrome to be run on 9 to 1 motors, which typically have an extremely hot exhaust gas. MCS can also be used inside of a header to reduce the amount of heat that is transfered into the metal of the header itself. MCS is an extremely effective thermal barrier. Use TLHB on chrome headers to reduce blueing. The end result of a coated manifold or header will be better performance, better appearance, reduced corrosion which means long-term improvement in appearance and will reduce component and underhood temperatures.
More information can be found at http://www.engineceramics.com/
Exhaust manifolds can either be a cast iron, factory-type manifold or a tube steel header typically used in performance applications, though they are becoming very common in OEM applications. There are a variety of reasons for coating an exhaust manifold header. #1 Corrosion protection. The manifold will live longer as well as look nicer. Whether it is for performance or show, coating an exhaust manifold is valuable to you. #2 The coating is a thermal barrier, thus keeping heat within the manifold or header. There are a number of benefits for this. First, by keeping heat within the manifold, you're going to accelerate the exhaust gas velocity which reduces back pressure and reduces fuel contamination due to reversion. This is a performance benefit. Second, you'll reduce the surface temperature of the manifold. This means if a person comes in contact with it, they are less likely to be burned and leave skin behind. If there is a component close to it, it will not see as much heat as it would with an uncoated manifold. In addition, not as much heat will be radiated under the hood or into the engine compartment. This reduces the underhood temperature which, again, reduces the temperature of surrounding parts, such as, alternators and starters. It also reduces the amount of heat that can be drawn in through the carburetor, which is a secondary performance benefit. There are a variety of coatings that can be used on exhaust manifolds or headers.
The most popular is our Cermakrome. This gives a near-chrome finish, tremendous corrosion protection and is an excellent thermal barrier. On the stock side, our Color-guard Cast Iron is extremely popular, especially with restorers, since it imparts an original, dark cast iron appearance rather than the lighter appearance that is more typical of a bead-blasted finish, which is not truly stock. If someone prefers a lighter appearance, they can mix our Colorguard Cast Iron with our Colorguard Aluminum to arrive at a shade they prefer. Both of these coatings have good thermal stability and are good thermal barriers. We recommend on cast iron, due to it's porosity, that a base coat of Cermakrome be put down first, then bake, then lightly sand blast, then put the color you wish on top. For tube steel headers, you can use our Cermakrome, Colorguard over a base coat, Black Satin, WBX, or WBLX. In most cases a single coating is acceptable. In extreme cases it might be advisable to use a base coat, such as our HHBK with a top coat such as Black Satin or WBX. In addition, you can put down a base coat of the HHBK, top coat it with WBX, and top coat that with our Cerma Clear, creating a glossy black finish that has very good high temperature stability.
We also manufacture an insulating base coat for performance applications where Cermakrome is desired. This is our MCS coating. This can be applied to the outside of the exhaust manifold or header, cured, lightly sand blasted, then a layer of Cermakrome applied over it, cured and polished. This will impart higher temperature capability allowing Cermakrome to be run on 9 to 1 motors, which typically have an extremely hot exhaust gas. MCS can also be used inside of a header to reduce the amount of heat that is transfered into the metal of the header itself. MCS is an extremely effective thermal barrier. Use TLHB on chrome headers to reduce blueing. The end result of a coated manifold or header will be better performance, better appearance, reduced corrosion which means long-term improvement in appearance and will reduce component and underhood temperatures.
More information can be found at http://www.engineceramics.com/
Coating a Crankshaft
Coating Crankshafts
There are two primary reasons for coating a crankshaft. Coatings provide increased lubrication to the journals and aid in shedding oil from the counterweights. Depending on the intended use, a different coating may be required for the counterweights.
The crank journals should be coated with a Dry Film Lubricant. Either DFL-1, TLML or CERMALUBE may be used. CERMALUBE may be the best to use since it cures to a thinner film than either DFL-1 or TLML. In all cases, reduce any excessive build up with Scotch Bright or similar material; DO NOT assemble the crank and bearings "tight". Properly done, there should be no need to change the clearances to allow for the coating. The coating will burnish to a near "0" dimension during running.
By coating with a dry film lubricant, you increase the lubrication levels, reducing friction and adding a protective layer. Normally lubrication is provided by a film of oil. The rotational action of a crank coupled with the pressure-fed oiling system, aids in keeping a film of oil in place at higher pressures. However, when pressures exceed what the oil can carry, the oil will flow away from the point of contact. All of TECH LINE'S Dry Film Coatings can lubricate at pressures exceeding 350,000 PSI which is well beyond the pressure you would expect to see in use. In addition, the coatings are "fluid retaining" and help keep a layer of oil in place. The coating actually becomes more lubricious or slippery as pressure increases, which enhances the protective, friction-reducing action.
The type of lubricating solids used will have a major effect on the ability of the coating to provide the desired protection. Certain ingredients such as "Teflon" are very slick only at low pressures and rotational speeds. Traditional lubricants like Graphite do not lubricate in environments where moisture is not present. Tech Line utilizes Moly (Molybdenum Disulfide, MOS2) as well as other extreme pressure lubricants that can carry tremendous loads while experiencing extremely fast rotational or sliding speeds. The resin must also be capable of maintaining a bond under the same conditions.
The counter weights can be coated with either TLTD or TLLB. Both these coatings have good oil shedding characteristics. TLTD will be used in most cases as it not only sheds oil but helps cool the crank by transferring the heat generated in the crank to the oil more rapidly. TLLB should only be used in Drag Racing or similar applications where the engine will only be run for a short period of time. TLLB is a thermal barrier like "Teflon" and other "polymers" and will actually trap heat in the crank
More information can be found at http://www.engineceramics.com/
There are two primary reasons for coating a crankshaft. Coatings provide increased lubrication to the journals and aid in shedding oil from the counterweights. Depending on the intended use, a different coating may be required for the counterweights.
The crank journals should be coated with a Dry Film Lubricant. Either DFL-1, TLML or CERMALUBE may be used. CERMALUBE may be the best to use since it cures to a thinner film than either DFL-1 or TLML. In all cases, reduce any excessive build up with Scotch Bright or similar material; DO NOT assemble the crank and bearings "tight". Properly done, there should be no need to change the clearances to allow for the coating. The coating will burnish to a near "0" dimension during running.
By coating with a dry film lubricant, you increase the lubrication levels, reducing friction and adding a protective layer. Normally lubrication is provided by a film of oil. The rotational action of a crank coupled with the pressure-fed oiling system, aids in keeping a film of oil in place at higher pressures. However, when pressures exceed what the oil can carry, the oil will flow away from the point of contact. All of TECH LINE'S Dry Film Coatings can lubricate at pressures exceeding 350,000 PSI which is well beyond the pressure you would expect to see in use. In addition, the coatings are "fluid retaining" and help keep a layer of oil in place. The coating actually becomes more lubricious or slippery as pressure increases, which enhances the protective, friction-reducing action.
The type of lubricating solids used will have a major effect on the ability of the coating to provide the desired protection. Certain ingredients such as "Teflon" are very slick only at low pressures and rotational speeds. Traditional lubricants like Graphite do not lubricate in environments where moisture is not present. Tech Line utilizes Moly (Molybdenum Disulfide, MOS2) as well as other extreme pressure lubricants that can carry tremendous loads while experiencing extremely fast rotational or sliding speeds. The resin must also be capable of maintaining a bond under the same conditions.
The counter weights can be coated with either TLTD or TLLB. Both these coatings have good oil shedding characteristics. TLTD will be used in most cases as it not only sheds oil but helps cool the crank by transferring the heat generated in the crank to the oil more rapidly. TLLB should only be used in Drag Racing or similar applications where the engine will only be run for a short period of time. TLLB is a thermal barrier like "Teflon" and other "polymers" and will actually trap heat in the crank
More information can be found at http://www.engineceramics.com/
Coating Engine Bearings
Coating Bearings
Lubricating and maintaining such lubrication is critical to the life of the bearing. A bearing is designed to carry tremendous loads while also being soft enough to allow small particles to "embed" in the bearing material. The various designs of bearings all address these primary needs. In addition, a bearing is a sacrificial part, in that it is easier and less expensive to replace bearings due to wear, than to replace the crankshaft.
Tech Line designed DFL-1 primarily as a bearing coating. Coatings come in two basic formulations; Solid Film and Dry Film. While the two terms can be and are to a great extent interchangeable, when it comes to bearings, the differences are important. A Solid Film lubricant derives it's name from the resin film formed during curing. This film has greater internal bond strength than the bond to the substrate, in this case the bearing. A Dry Film, on the other hand, has a weaker internal bond than the bond to the substrate. When these features are applied to a bearing, the Dry Film is superior.
Since no coating is a 100% friction-free material, some pressure will be exerted against the coatings. In a rotational application, such as we are discussing, the coating needs to be able to MINIMALLY flake away when such pressure is reached. Otherwise, the coating can delaminate. DFL-1 functions in this manner. Generally the particle size that can be removed is under 1 micron.
The coating is capable of withstanding pressures in excess of 350,000 psi while lubricating. This is well beyond the strength of the bearing itself. As pressure increases the coating actually becomes more lubricious. In addition, DFL-1 is a "fluid retaining" material that actually holds oil in place on the bearing.
One of the most important features of DFL-1 is it's ability to maintain it's full lubrication characteristics even in extremely thin films. DFL-1 typically will be applied in a film thickness of from .0003" to .001". Obviously this would affect clearances when the film approaches .001". After checking the thickness, burnish with "Scotchbright" or similar material until the film thickness is no more than .0003". During running, the coating will burnish to a near "0" dimension. This characteristic allows the bearing to be run with it's normal installed clearance. Coatings that form a "harder" film will also reduce friction and provide a protective layer to the bearing, however, as these coatings begin to wear , clearances will open up. DFL-1 does not have this problem.
Due to the above features, DFL-1 can extend the life of a bearing while reducing friction, particularly in instances where normal oil film failure could lead to bearing failure. DFL-1 is an easy to apply, water based material that has a low cure temperature of 300F. It can be sprayed or brushed, though a spray application is recommended for best results.
More information can be found at http://www.engineceramics.com/
Lubricating and maintaining such lubrication is critical to the life of the bearing. A bearing is designed to carry tremendous loads while also being soft enough to allow small particles to "embed" in the bearing material. The various designs of bearings all address these primary needs. In addition, a bearing is a sacrificial part, in that it is easier and less expensive to replace bearings due to wear, than to replace the crankshaft.
Tech Line designed DFL-1 primarily as a bearing coating. Coatings come in two basic formulations; Solid Film and Dry Film. While the two terms can be and are to a great extent interchangeable, when it comes to bearings, the differences are important. A Solid Film lubricant derives it's name from the resin film formed during curing. This film has greater internal bond strength than the bond to the substrate, in this case the bearing. A Dry Film, on the other hand, has a weaker internal bond than the bond to the substrate. When these features are applied to a bearing, the Dry Film is superior.
Since no coating is a 100% friction-free material, some pressure will be exerted against the coatings. In a rotational application, such as we are discussing, the coating needs to be able to MINIMALLY flake away when such pressure is reached. Otherwise, the coating can delaminate. DFL-1 functions in this manner. Generally the particle size that can be removed is under 1 micron.
The coating is capable of withstanding pressures in excess of 350,000 psi while lubricating. This is well beyond the strength of the bearing itself. As pressure increases the coating actually becomes more lubricious. In addition, DFL-1 is a "fluid retaining" material that actually holds oil in place on the bearing.
One of the most important features of DFL-1 is it's ability to maintain it's full lubrication characteristics even in extremely thin films. DFL-1 typically will be applied in a film thickness of from .0003" to .001". Obviously this would affect clearances when the film approaches .001". After checking the thickness, burnish with "Scotchbright" or similar material until the film thickness is no more than .0003". During running, the coating will burnish to a near "0" dimension. This characteristic allows the bearing to be run with it's normal installed clearance. Coatings that form a "harder" film will also reduce friction and provide a protective layer to the bearing, however, as these coatings begin to wear , clearances will open up. DFL-1 does not have this problem.
Due to the above features, DFL-1 can extend the life of a bearing while reducing friction, particularly in instances where normal oil film failure could lead to bearing failure. DFL-1 is an easy to apply, water based material that has a low cure temperature of 300F. It can be sprayed or brushed, though a spray application is recommended for best results.
More information can be found at http://www.engineceramics.com/
Coating a Valve
Coating a Valve
WHY coat a valve? The purpose behind coating a valve is to extend the part life and reduce friction. You're dealing with an intake valve and an exhaust valve. We'll look at the intake valve first.
The INTAKE valve seals the combustion chamber on the intake port side of the head. Prior to that, it is opening to allow air and fuel to enter the combustion chamber. In take valves usually do not suffer as severely as exhaust valves which see combustion chamber temperatures. Therefore, the primary concern is lubricating the valve stem and seat. We do this by the application of a dry film lubricant such as DFL-1, TLML, or CERMA LUBE. This reduces the friction particularily in engines where oil flow is restricted to the head. The dry film takes over the bulk of the lubrication chore. It is still advisable to coat the face of the valve in the combustion chamber to help retain combustion chamber heat in the chamber. This also reduces the operating temperature of the valve. It reduces the temperature of the back of the valve so the incoming air fuel mix does not pick up as much heat from the valve, as it would, if it were uncoated. Normally, it is not necessary to thermal barrier coat the back of the valve, though, it can be done if you wish. Typically, the face is thermal barrier coated with CBC2 or CBX; the back and stem are dry film coated with DFL-1, TLML or CERMA LUBE.
On the EXHAUST side we have a more severe environment because the valve is seeing combustion chamber temperatures, which on a normally asperated engine, can easily be at 1350F; on certain engines this can run even higher. So we definitely coat the face of the valve with a thermal barrier ( CBC2 or CBX ) to reduce the heat that the valve absorbes. Then coat the back of the stem with a dry film lubricant ( DFL-1, TLML or CERMA LUBE ). Again, it's very critical on the exhaust valve stem because the heat can reduce the ability of your oil to lubricate. Consequently, the permanently bonded, high pressure, high temperature lubricants work extremely well at reducing friction and wear on the valve and the guide. In some cases, it is advisable to coat the back of the exhaust valve such as on a Titanium valve where you can have metal erosion due to hot gas and flame passing over the raw Titanium. ( CBC2 or CBX ). On other valves it is still preferable to coat the back with the dry film ( DFL-1, TLML or CERMA LUBE ) to contribute to carbon shedding so you do not get a carbon build-up on the back of the valve which can create turbulance in the exhaust flow.
Also, by coating the back on both the intake and exhaust valve after all machine work is done, you permanently bond the lubricant to the areas that will contact the valve seat thus reducing wear in this area and creating a better long term seal.
More information can be found at http://www.engineceramics.com/
WHY coat a valve? The purpose behind coating a valve is to extend the part life and reduce friction. You're dealing with an intake valve and an exhaust valve. We'll look at the intake valve first.
The INTAKE valve seals the combustion chamber on the intake port side of the head. Prior to that, it is opening to allow air and fuel to enter the combustion chamber. In take valves usually do not suffer as severely as exhaust valves which see combustion chamber temperatures. Therefore, the primary concern is lubricating the valve stem and seat. We do this by the application of a dry film lubricant such as DFL-1, TLML, or CERMA LUBE. This reduces the friction particularily in engines where oil flow is restricted to the head. The dry film takes over the bulk of the lubrication chore. It is still advisable to coat the face of the valve in the combustion chamber to help retain combustion chamber heat in the chamber. This also reduces the operating temperature of the valve. It reduces the temperature of the back of the valve so the incoming air fuel mix does not pick up as much heat from the valve, as it would, if it were uncoated. Normally, it is not necessary to thermal barrier coat the back of the valve, though, it can be done if you wish. Typically, the face is thermal barrier coated with CBC2 or CBX; the back and stem are dry film coated with DFL-1, TLML or CERMA LUBE.
On the EXHAUST side we have a more severe environment because the valve is seeing combustion chamber temperatures, which on a normally asperated engine, can easily be at 1350F; on certain engines this can run even higher. So we definitely coat the face of the valve with a thermal barrier ( CBC2 or CBX ) to reduce the heat that the valve absorbes. Then coat the back of the stem with a dry film lubricant ( DFL-1, TLML or CERMA LUBE ). Again, it's very critical on the exhaust valve stem because the heat can reduce the ability of your oil to lubricate. Consequently, the permanently bonded, high pressure, high temperature lubricants work extremely well at reducing friction and wear on the valve and the guide. In some cases, it is advisable to coat the back of the exhaust valve such as on a Titanium valve where you can have metal erosion due to hot gas and flame passing over the raw Titanium. ( CBC2 or CBX ). On other valves it is still preferable to coat the back with the dry film ( DFL-1, TLML or CERMA LUBE ) to contribute to carbon shedding so you do not get a carbon build-up on the back of the valve which can create turbulance in the exhaust flow.
Also, by coating the back on both the intake and exhaust valve after all machine work is done, you permanently bond the lubricant to the areas that will contact the valve seat thus reducing wear in this area and creating a better long term seal.
More information can be found at http://www.engineceramics.com/
Coating an Intake Manifold
Coating an Intake Manifold
There are two reasons for coating an intake manifold. The first would be Performance, the second Appearance. Let's discuss Performance first.
In this instance, you are dealing with heat that is generated by the engine. You will also acquire heat from the hot oil that may be tossed up under the underside of the intake manifold. This means we want to apply a thermal barrier ( TLLB, CBC2, CBX, MCX ) to the bottom of the intake manifold, the flange area where it would bolt to the head and also the flange area where the carburetor would bolt to the intake manifold. This will reduce the amount of heat that enters the manifold itself, keeping the manifold cooler. Typically, a normally aspirated engine will see a 1% improvement in power for every 10 degree drop in carb air inlet temperature. A Turbo charged engine will see a 2% increase. Keeping the manifold cooler than normal allows an engine to generate more horse power. In addition to this, you would coat the top of the manifold with a thermal dispersant such as our TLTD. This means that the heat that does get into the intake manifold will be more rapidly dispersed into the air moving over it, thus cooling the intake manifold further. This gives you a greater chance of creating more horse power by reducing the inlet temperature. You can also coat the inside of the runners in an intake manifold. You can use 1 or 2 coatings. A single coating that we recommend would be our dry film ( DFL-1, TLML or CERMA LUBE ). These are known as 'fluid retaining coatings' and the fuel/air mix as it passes through an intake manifold on a carbureted engine is treated like a 'fluid in motion'. The coating will have a tendency to create a small amount of boundary layer turbulence which will reduce fuel drop-out. You may also apply a thermal barrier to the inside of a runner first, then the dry film over it. If you're doing this, we recommend using our TLLB with TLML over the top of it. You not only create the boundary layer turbulence, you further reduce the amount of heat that does enter the fuel/air mix.
On the cosmetic side, while the TLTD is a very nice-looking coating, it is Black. If someone is looking for more show and they like a bright, polished appearance, then Cermakrome, as an example, can be used. Since Cermakrome is a thermal barrier, we recommend that you coat the bottom and the top. In this way, while you're inhibiting the amount of heat that can be dispersed from the top of the manifold because of it being coated, you're reducing the amount of heat that can be absorbed by the manifold because of the same coating on the bottom. Thus, you are at least creating an equilibrium and not dealing with a heat problem. The coating is extremely high temperature resistant, does not blue or discolor like chrome, does not oxidize significantly as a polished aluminized surface will, so you can maintain a very nice, high-polished surface not affected by fuel oils and solvents.
More information can be found at http://www.engineceramics.com/
There are two reasons for coating an intake manifold. The first would be Performance, the second Appearance. Let's discuss Performance first.
In this instance, you are dealing with heat that is generated by the engine. You will also acquire heat from the hot oil that may be tossed up under the underside of the intake manifold. This means we want to apply a thermal barrier ( TLLB, CBC2, CBX, MCX ) to the bottom of the intake manifold, the flange area where it would bolt to the head and also the flange area where the carburetor would bolt to the intake manifold. This will reduce the amount of heat that enters the manifold itself, keeping the manifold cooler. Typically, a normally aspirated engine will see a 1% improvement in power for every 10 degree drop in carb air inlet temperature. A Turbo charged engine will see a 2% increase. Keeping the manifold cooler than normal allows an engine to generate more horse power. In addition to this, you would coat the top of the manifold with a thermal dispersant such as our TLTD. This means that the heat that does get into the intake manifold will be more rapidly dispersed into the air moving over it, thus cooling the intake manifold further. This gives you a greater chance of creating more horse power by reducing the inlet temperature. You can also coat the inside of the runners in an intake manifold. You can use 1 or 2 coatings. A single coating that we recommend would be our dry film ( DFL-1, TLML or CERMA LUBE ). These are known as 'fluid retaining coatings' and the fuel/air mix as it passes through an intake manifold on a carbureted engine is treated like a 'fluid in motion'. The coating will have a tendency to create a small amount of boundary layer turbulence which will reduce fuel drop-out. You may also apply a thermal barrier to the inside of a runner first, then the dry film over it. If you're doing this, we recommend using our TLLB with TLML over the top of it. You not only create the boundary layer turbulence, you further reduce the amount of heat that does enter the fuel/air mix.
On the cosmetic side, while the TLTD is a very nice-looking coating, it is Black. If someone is looking for more show and they like a bright, polished appearance, then Cermakrome, as an example, can be used. Since Cermakrome is a thermal barrier, we recommend that you coat the bottom and the top. In this way, while you're inhibiting the amount of heat that can be dispersed from the top of the manifold because of it being coated, you're reducing the amount of heat that can be absorbed by the manifold because of the same coating on the bottom. Thus, you are at least creating an equilibrium and not dealing with a heat problem. The coating is extremely high temperature resistant, does not blue or discolor like chrome, does not oxidize significantly as a polished aluminized surface will, so you can maintain a very nice, high-polished surface not affected by fuel oils and solvents.
More information can be found at http://www.engineceramics.com/
Spray -On Horsepower, Ceramic Coatings
Spray-On horsepowerCeramic Coatings
By Bob Ryder Who would have thought that horsepower could be gained from coating internal engine components? Internal engine components are made from dissimilar metals. Due to the lack of metallurgical similarities of these components, they absorb and dissipate heat at different cycling periods. The ability to protect and cool engine internal and external components actually contributes to noticeable horsepower and performance gains. The three major contributors to horsepower gain are heat resistance, friction reduction, and wear protection. Over the years, performance engine builders have been refining the leading edge of horsepower gains while experimenting with ceramic coatings. Ceramic coatings are used as a barrier between dissimilar metals to reduce friction, which cause heat, creating unwanted wear of internal engine components. By applying ceramic coatings to these dissimilar metal components, it will allow them to interface with one another more uniformly and compatibly. Prior to applying ceramic coatings to components, its surfaces must be prepped by media- or sandblasting. This will remove the component's outer crust surface and any contaminants, exposing the virgin metal underneath. Some feel that it is important to heat the component in an oven after it has been media- or sandblasted, to sweat out any additional contaminants or porosity from within its metallurgical molecular structure. If not, during the initial time the component is exposed to a heat cycle, some porosity may sweat to the surface and become trapped underneath the coated surface, causing the coated surface to de-laminate. It is very important for the component to be pure and clean before applying ceramic coatings. Ceramic coatings are available in a variety of coatings, including tungsten and titanium. The ceramic coatings are applied with an automotive detail touch-up gravity-fed spray gun with a nozzle size of about 0.8 inch, because its smaller size allows for better control. Most ceramic coatings are applied at 35 to 40 psi for solvent coatings and 50 to 60 psi for water-based coatings. It is best to apply ceramic coatings inside a spray paint booth using a respirator when using solvent- or water-based coatings. The ceramic viscosity, or thickness, is very thin and must be applied carefully, so it will not run. Most ceramic film application buildup is approximately 0.0003 to 0.001 inch. After the component is coated, it is inspected for uniform coverage, then allowed to air dry at room temperature to slowly begin the solvent- or water-based evaporation process, before placement in an oven to cure. It is best that the components are dried in an upright air-circulating oven to allow even heating for uniform curing of the component. The first increment of heat is 175 degrees Fahrenheit during ambient versus curing temperature transition for about 10 minutes, then cranked up to a cure temp of 600 degrees Fahrenheit for one hour. When building up a film barrier to 0.001 inch, this would affect clearances. After applying the ceramic film, the thickness is checked, then burnished with a ScotchBrite pad or similar material until the film thickness is no less than 0.0003 inch. This will allow the bearings to be run with its normal installed clearance. To polish Cermakrome coatings of exhaust manifolds and headers, it is best to use a vibrator type of polisher using Microbright ceramic balls and the appropriate polishing compound. The most common applications for ceramic coatings are on the exhaust system, manifolds, and headers. When ceramic thermal barrier coatings are applied to exhaust manifolds or headers, they provide two advantages. They protect the headers from rust and corrosion and also reduce heat loss, which translates into high power output. If the headers are internally coated, they will create a higher velocity of the hot exhaust gases and less turbulence due to a smoother surface. Pistons can also increase their performance characteristics with ceramic coatings. Coating the piston's crown and top will cause heat reflectivity, driving a percentage of any detonation energy back into the fuel burn zone, to increase fuel burn efficiency. It will also lower carbon buildup, which reduces detonation quality, as it builds up on the piston's crown and increases the risk of detonation damage to the piston crown surface. By protecting the crown and land diameter surfaces, it will allow for a leaner fuel mixture. Piston skirts can be coated to create an excellent dry sliding surface during engine start-up and will help eliminate skirt slap during initial engine run-in. Using a dry coating will fight against scuffing and abrasion of the piston skirt during its stroke travel inside the engine block cylinder. The inside of the piston can also be coated with an oil-shedding coating to cut parasitic drag and return oil to the sump faster. Ceramic coatings can also be applied over the piston ring contact face of OEM hard chromium, which provides lowering friction between the ring face and cylinder inner bore surface scuffing, and also improves wear resistance. Ceramic-coating the cylinder head's combustion chamber and exhaust ports will create a faster, hotter burn and help scavenge gases at a faster rate. The coating of these passages also creates thermal transfer from hot gases to the heads themselves. The cylinder head valley can be covered with an oil-shedding coating to speed the return to the sump. Some will coat the cylinder head's external surface with a thermal dispersant to aid in cooling the head. The valve-springs are coated with an oil-shedding ceramic to aid in the oil return to the sump. Camshaft bearing surfaces are not treated, but the rest of the camshaft is coated with a dry film lubricant. The crankshaft and connecting rods are sprayed with the oil-shedding coating to cut parasitic drag.An intake manifold is coated on the bottom with an oil-shedding coating to cut thermal heat transfer from the oil to the intake charge. It also helps eliminate fuel puddling on the intake manifold's internal floor surface. If the intake manifold floor is made too slick, it can hinder fuel and air atomization, not allowing the fuel and air mixture from tumbling, keeping the two suspended. The intake manifold's exterior can be ceramic-coated to reduce heat penetration, maintaining a cooler air/fuel mixture. Ceramic coatings have proven themselves in engine horsepower gain by reducing friction, heat, and wear.
More information can be found at http://www.engineceramics.com/
By Bob Ryder Who would have thought that horsepower could be gained from coating internal engine components? Internal engine components are made from dissimilar metals. Due to the lack of metallurgical similarities of these components, they absorb and dissipate heat at different cycling periods. The ability to protect and cool engine internal and external components actually contributes to noticeable horsepower and performance gains. The three major contributors to horsepower gain are heat resistance, friction reduction, and wear protection. Over the years, performance engine builders have been refining the leading edge of horsepower gains while experimenting with ceramic coatings. Ceramic coatings are used as a barrier between dissimilar metals to reduce friction, which cause heat, creating unwanted wear of internal engine components. By applying ceramic coatings to these dissimilar metal components, it will allow them to interface with one another more uniformly and compatibly. Prior to applying ceramic coatings to components, its surfaces must be prepped by media- or sandblasting. This will remove the component's outer crust surface and any contaminants, exposing the virgin metal underneath. Some feel that it is important to heat the component in an oven after it has been media- or sandblasted, to sweat out any additional contaminants or porosity from within its metallurgical molecular structure. If not, during the initial time the component is exposed to a heat cycle, some porosity may sweat to the surface and become trapped underneath the coated surface, causing the coated surface to de-laminate. It is very important for the component to be pure and clean before applying ceramic coatings. Ceramic coatings are available in a variety of coatings, including tungsten and titanium. The ceramic coatings are applied with an automotive detail touch-up gravity-fed spray gun with a nozzle size of about 0.8 inch, because its smaller size allows for better control. Most ceramic coatings are applied at 35 to 40 psi for solvent coatings and 50 to 60 psi for water-based coatings. It is best to apply ceramic coatings inside a spray paint booth using a respirator when using solvent- or water-based coatings. The ceramic viscosity, or thickness, is very thin and must be applied carefully, so it will not run. Most ceramic film application buildup is approximately 0.0003 to 0.001 inch. After the component is coated, it is inspected for uniform coverage, then allowed to air dry at room temperature to slowly begin the solvent- or water-based evaporation process, before placement in an oven to cure. It is best that the components are dried in an upright air-circulating oven to allow even heating for uniform curing of the component. The first increment of heat is 175 degrees Fahrenheit during ambient versus curing temperature transition for about 10 minutes, then cranked up to a cure temp of 600 degrees Fahrenheit for one hour. When building up a film barrier to 0.001 inch, this would affect clearances. After applying the ceramic film, the thickness is checked, then burnished with a ScotchBrite pad or similar material until the film thickness is no less than 0.0003 inch. This will allow the bearings to be run with its normal installed clearance. To polish Cermakrome coatings of exhaust manifolds and headers, it is best to use a vibrator type of polisher using Microbright ceramic balls and the appropriate polishing compound. The most common applications for ceramic coatings are on the exhaust system, manifolds, and headers. When ceramic thermal barrier coatings are applied to exhaust manifolds or headers, they provide two advantages. They protect the headers from rust and corrosion and also reduce heat loss, which translates into high power output. If the headers are internally coated, they will create a higher velocity of the hot exhaust gases and less turbulence due to a smoother surface. Pistons can also increase their performance characteristics with ceramic coatings. Coating the piston's crown and top will cause heat reflectivity, driving a percentage of any detonation energy back into the fuel burn zone, to increase fuel burn efficiency. It will also lower carbon buildup, which reduces detonation quality, as it builds up on the piston's crown and increases the risk of detonation damage to the piston crown surface. By protecting the crown and land diameter surfaces, it will allow for a leaner fuel mixture. Piston skirts can be coated to create an excellent dry sliding surface during engine start-up and will help eliminate skirt slap during initial engine run-in. Using a dry coating will fight against scuffing and abrasion of the piston skirt during its stroke travel inside the engine block cylinder. The inside of the piston can also be coated with an oil-shedding coating to cut parasitic drag and return oil to the sump faster. Ceramic coatings can also be applied over the piston ring contact face of OEM hard chromium, which provides lowering friction between the ring face and cylinder inner bore surface scuffing, and also improves wear resistance. Ceramic-coating the cylinder head's combustion chamber and exhaust ports will create a faster, hotter burn and help scavenge gases at a faster rate. The coating of these passages also creates thermal transfer from hot gases to the heads themselves. The cylinder head valley can be covered with an oil-shedding coating to speed the return to the sump. Some will coat the cylinder head's external surface with a thermal dispersant to aid in cooling the head. The valve-springs are coated with an oil-shedding ceramic to aid in the oil return to the sump. Camshaft bearing surfaces are not treated, but the rest of the camshaft is coated with a dry film lubricant. The crankshaft and connecting rods are sprayed with the oil-shedding coating to cut parasitic drag.An intake manifold is coated on the bottom with an oil-shedding coating to cut thermal heat transfer from the oil to the intake charge. It also helps eliminate fuel puddling on the intake manifold's internal floor surface. If the intake manifold floor is made too slick, it can hinder fuel and air atomization, not allowing the fuel and air mixture from tumbling, keeping the two suspended. The intake manifold's exterior can be ceramic-coated to reduce heat penetration, maintaining a cooler air/fuel mixture. Ceramic coatings have proven themselves in engine horsepower gain by reducing friction, heat, and wear.
More information can be found at http://www.engineceramics.com/
Thermal Coatings by Don Redmon
Thermal Coatings
-Don Redmon
The following is a brief and general customer’s guide to Thermal Coatings. Thermal and friction reducing applications are applied after the part is etched. The part is cleaned, the coating is applied and then oven cured. This insures that the application, unlike paint, is tougher and more than skin deep.
The semi-gloss black external coating is a Thermal Dispersant, it gets rid of heat faster and more efficiently than bare metal, it also sheds mud and rubber. Typical applications are cylinders, cylinder heads, intake manifolds, brake calipers, radiators and oil coolers. Always properly warm up your engine before operational loading. It will now take longer for your engine to come to operating temperature. Clean with soap, water and/or light solvents, do not leave it to soak in a solvent tank.
The silvery looking Thermal Barrier coating keeps heat from passing through it. It is applied to piston crowns, combustion chambers, valve faces and exhaust pipes, to name just a few uses. This coating will raise the working temperature inside of the combustion chamber. We suggest that you start with a colder range spark plug and watch your readings, this is especially important the smaller the bore size. Clean carefully, do not scrape the surface, polish with extra fine steel wool using light pressure.
The dark gray application is a Dry Film Lubricant. It is used on piston skirts, bearings and valve springs. This is the softest of the coatings and depending on the clearances, it will visually wear. Use light compatible oil when installing a piston in a cylinder. Remember though that the applications are more than skin deep.
Depending on engine modifications, your location, air pressure and quality, etc., you may need to re-adjust or re-jet your engines fuel and ignition systems. Do this carefully, i.e. richer and retarded is better to start with. Always err on the side of caution, it is much less costly. Please do not hesitate to call with any questions you may have.
Hello, my name is Don Redmon and I am the owner of Replika Maschinen, Inc. We are an airflow, porting, engine and thermal coating facility located in the Santa Cruz, California area. I have been professionally involved in the racing, high performance and technical automotive and motorcycle markets for over a quarter of a century.
I was recently honored when asked to write a column for "Speedoptions.com". This column will cover a wide variety of technical subjects and I welcome your comments and suggestions for possible future columns. If there is something of a technical nature you would like to know more about, let us know. In the meantime you can expect to see future articles on:Engine blueprinting, what it is and why I should care.Cylinder heads, competition valve jobs, various stages of porting, and types of porting.Thermal coatings, cryogenics, various types of dynamometers and what the differences are.Turbochargers, superchargers, nitrous oxide, where these devices come from and what we should be doing with them.We will also talk about camshafts and the largely ignored valve spring. I will get into basic subjects such as gasolines, octane's and both pump and racing fuels and why you should care. What the differences are between gasoline, methanol and nitro methane. Multi valved and multi camed cylinder heads, fuel injection, how new is this technology really, and where it comes from.
But most of all, this column will be about information. There are many products and services out their vying for your hard earned dollars. Some products and services are good choices while others are less than good or less than optimum for what you are trying to accomplish. Only when primed with some basic knowledge and hopefully the spark to seek out additional information, can you then venture forth, as a better-informed and more questioning consumer. Therefore, our first topic will be about selecting symbiotic and workable combinations, a continually overlooked but very important aspect of engine building. As we are an air flow/ porting facility, we deal with many different types of internal combustion engines and racing disciplines. Two strokes for motocross and road racing, four strokes, high output and high revving automotive and motorcycles, Imports to big cubic inch Domestic V-8's. We even work with low revving, very high torque, large capacity diesel engines improving power and fuel efficiency. However, no matter what we are doing or whom we are working with we hear the same story again and again, a story every shop in existence has heard and experienced frequently. It goes like this: The consumer calls or comes in with a box of different parts all by different manufactures. The customer then proceeds to ask to have this menagerie assembled into an engine that will propel his vehicle into the 6-second zone.
Marketing in this country is an art form. If you doubt this, consider the pet rock, or grass growing plaster gargoyles and professional wrestling. We are the world leaders in marketing and packaging of products. My point here is that just because something looks good, comes in a great package and promises you straight teeth and a better sex life, it does not mean that it is what you need in your particular car or that it will work with your particular engine combination. Engines, like people, are made up of various component parts. These parts must work in harmony in order to receive the greatest return from the effort put into them. The better the parts work together, the greater the harmony, the greater the output of power. Trying the throwing mud at the wall and then seeing what sticks approach to component selection is not a wise path to follow. So before you buy, formulate a plan of action as to what you want to sensibly achieve and what you can afford to achieve. Then, contact the companies and shops you would like to be working with on your project and ask their advice. Contact others and get their advice, read about your engine, go to the races and ask questions. Then, with your engine builder's help, make sensible realistic decisions and purchases. Always purchase quality components. Remember you get what you pay for.
At Replika Maschinen, inc. our primary business is improving airflow and volumetric efficiency primarily via porting of the engines air passageways. However, we also seek to improve volumetric efficacy by improving the quality of the air or fluid charge by lowering the temperature of that charge to gain more oxygen per volume. Air is the working fluid of internal combustion engines, so air is the fluid I am referring to here. When we lower the temperature of our working fluid/air, it becomes more dense. One of the ways in which we lower the temperature of the inlet charge and engine and achieve this volumetric advantage is through the world of THERMAL COATINGS. Around the end of the Second World War the need to go higher, further, faster enveloped the defense and aeronautical industries. These desires spawned a metallurgical revolution in exotic materials. But along with these exotic materials for air frames and more powerful engines came new problems of protection. Corrosion resistance, noise suppression, friction reducers, thermal barriers and thermal dispersants were invented or modified to address these new concerns. The automotive racing industry discovered these substances sometime in the 1970's. However, as they soon learned, racecars and their engines are not jet-propelled aircraft and vice-versa. Coatings that worked just perfectly in the sustained and controlled environment of aerospace often meet its match in an automobile engine. Zirconia based ceramics for example, have very different expansion rates, 4.16x10-6, when compared to aluminum alloy at 13.7x10-6 over temperature ranges of 80 to 800 deg. F. Fortunately there were individuals who saw the benefits and worked hard to develop coatings specifically for the automotive industry. These are what we here at Replika Maschinen, inc. and other facilities around the world use and are what we will concern ourselves with as the topic of conversation to follow.
Turbo Compressor Housing
But first, what are thermal coatings and what do they do? Thermal coatings come in two basic categories; thermal dispersants to help get rid of heat and thermal barriers to block heat. Thermal dispersants help the coated part shed heat faster than that part normally would dispense with were it bare or un-coated. Thermal dispersants are generally exterior coatings and therefore primarily work via convection, but conduction is also involved. Convection is the transfer of heat by the laminar or turbulent motion of a liquid or a gas from one region of space to another. The convection style transference of heat as it relates to the automotive type world would include radiators, oil-coolers, brake calipers, rotor carriers and hubs, exhaust systems, turbocharger/supercharger housings and air and liquid cooled engines. Conduction is the transfer of thermal energy through a material or between two bodies in contact. This would apply to heat transfer between cylinder and cylinder head or any two or more parts in contact with one another. So for our pop quiz, which theory of thermal heat transference covers lap dancing.
Miata 1.6 Cylinder Head
THERMAL DISPERSANTS as the name implies, reduce or remove excessive heat. As mentioned earlier, a large majority of an engines potential heat energy ends up as waste. An engine must dispense with this excessive heat or else burn up. Coated cylinder heads dispose of excessive heat at a far greater rate then un-coated heads. Reducing the onset of engine killing detonation, lower intake charge temperatures and less chance of blowing head gaskets due to cylinder head warpage and walk are just a few more advantages. Engines work on heat but this heat must be properly dealt with. Too little and the engine will not operate in an efficient manner, too much and it will melt down. In early 1998, the INDY LITES organization decided to conduct a test of their then current oil cooler and thermal dispersants. They had the oil cooler thermal dispersant coated, it was then tested on and off the track. They experienced a 15% reduction in oil temperatures; the smaller older coated oil cooler out performed its newer and larger replacement. All INDY LITES teams now run coated oil coolers. In NASCAR, Bill Elliot and many others, run coated radiators to help reduce internal engine and engine bay temperatures and improve aerodynamics via smaller radiator openings. Brake parts and systems can also be coated. Obviously the faster heat is dissipated the less likely the chance of fade or out rite failure. As a side benefit, coated parts shed dirt and rubber and are far less likely to plug up, as readily as un-coated parts will. In our next article, we will discuss Thermal Dispersants and Dry Film Lubricants. Thanks, until next time, Don Redmon, Replika Maschinen, inc.
Stop Making Sense Thermal Coatings Part II Article by: Don Redmon (Friday, May 18, 2001) (522 reads)
Extra High Temperature Thermal Barrier Coated Expansion Chamber In part 2 of our article on thermal coatings, we will discuss Thermal Barriers and Dry Film Lubricants. Thermal barriers as the name implies are barriers or shields to thermal events or heat. An internal combustion engine is basically a thermally controlled air pump. So various engine events will depend on heat to function properly while others depend on the elimination of heat to live. Remember, an engine's working fluid is air, introduce an air charge into the combustion chamber, provide an ignition source with a combustible compound to heat it at the correct time, and you produce work. Sounds easy, however heat is the key to making a little power, a lot of power, or seizing the engine. Heat as it relates to a high performance racing engine is different conceptually from what is wanted by a smog controlled street engine. While the conceptual differences are there, as are the reasons for each argument, the results are similar. Combustion efficiency produces more work with less fuel and less residual emissions. Areas to hold heat into include, the combustion chamber and exhaust systems and areas to shed heat include most everything else. On the intake side, the cooler the intake air the more dense the air charge. However, there are instances, EPA, CARB environmental controls, evaporation levels of certain fuels, that demand higher but moderated temperatures. Controlling the heat of the combustion process and the exhaust elimination system can assist in maintaining control over both engine interior and exterior temperatures. An engine certainly does get hot under the hood. Studies have documented temperature drops of 100 to 300 degrees of under hood heat. What do you think dropping under hood temperature 100 degrees does to your inlet charge temperatures? Barrier coatings on exhaust system components contain the heat into the system and preclude the heat from just migrating around the semi-closed container called your engine bay. By controlling this engine heat, we put it to work for us in the area of power increases instead of simply an ambulatory road kill grill. I am sure you have all heard the term ceramics applied to automotive-coated parts. While ceramics are used in automotive applications, their use is still relatively new and cutting edge. In the "1980's" I remember magazine articles and talk about an "Oval Track" style "Midget" engine, designed, built and run using ceramics and plastics in place of steel and aluminum for internal engine parts. Ferrari and other Formula One teams are currently using ceramics in both engine and suspension applications. But for the average guy or gal on the street, their use is minimal outside of thermal barriers. Barrier coatings do contain amounts of ceramic but they are not pure ceramic for one very important reason, coefficient of expansion. Aluminum alloy for example, will expand at 13.7x 10(-6th) while zirconia based ceramics expand at 4.16x 10(-6th) in the temperature realms of 80 to 800 degrees Fahrenheit. Aluminum obviously expands at a far greater rate than does the ceramic, which makes it hard to keep them in contact with each other for very long. While steel headers for example, will expand less than aluminum, steel is still affected by heat more than and therefore its expansion rate is greater than the ceramic too. Coating pistons, valves, combustion chambers, turbocharger exhaust manifolds and turbine housings, exhaust ports, and exhaust headers and pipes is where thermal barrier coatings most useful work is done. Keeping the combustion heat into the combustion chamber where it belongs and not allowing it to migrate throughout the engine is important. As exhaust gas speed and wave intensity is directly related to temperature elevation and the consistency of the temperature throughout the length of the pipe. Maintaining elevated and constant temperature throughout the length of the system is paramount to effective scavenging and evacuation. Thermal barriers hold that heat into the system helping it to perform better and also protecting the coated parts from rust corrosion and premature damage. So where does all of that internally combusted heat go to? It goes to the same places it normally does but now we are trying to control and positively use the normally wasted heat energy. Normally, part will go into the cooling system to be eliminated via the radiator or in the case of air-cooled engines, cooling fins. Part will go out the exhaust system as additional waste. The remaining thirty percent or less is actually used to produce work and turn the crankshaft. It should not take a rocket scientist to realize that increasing the latter's percentage even in small amounts will garner additional returns in work and power. Here at Replika Maschinen, inc., we have found that coated pistons will stave off the damaging effects of uncontrolled excessive combustion chamber heat, detonation and/or pre-ignition. This could ordinarily lead to a hole in the piston in two strokes and/or ring land damage in a four-stroke engine. Thermal barrier coated pistons transfer less heat to wrist pins, cage bearings and the general crankcase area. Thermal barrier coated intake and exhaust valves will not transfer their normal amount of heat directly to the valve springs, hence the springs last far longer than normal. As the valves themselves do not get as hot, they do not wear the respective valve seat contact areas as quickly, parts last longer with less heat. Thermal barriers will not totally prevent engine damage caused by tuning errors that lead to severe detonation and or pre-ignition. They will not improve your sex life, eliminate problems caused by general ignorance and/or help from your friends who know everything or create world peace. However, they will protect vital internal engine components far longer and provide an extended range of extra protection when things do go wrong. By coating these parts, we hold the heat in to where it belongs, the combustion chamber. We gain usage of more of the potential and available BTU's (British Thermal Units a system of measuring heat potential) to use in order to convert our inlet charge to work. Heating the air to turn the crankshaft translates into the potential for more work and power. Dry Film Lubricants and friction reducers are lubricants that maintain themselves in a dry state. Friction is a force that resists motion between two bodies or parts in contact with one another. Lubrication is necessary to reduce friction and prevent metal to metal contact within your engine's various moving parts. A thin film of oil, sometimes only ". 000025 of an inch" thick is all that holds your engine parts apart and moving. Dry films work and provide protection at all times, however, they provide special lubricity and extra protection when combined with liquid lubricants. You might think of dry film lubricants, as you would think of freeze dried foods, you add liquid to make them work even better. Dry films are a mix of various very slick materials, in a resin-bonded matrix. The application process is similar to thermal coatings and the lubricants are imbedded into the metal. Dry film lubricants are designed to reduce friction, which produces heat. They also reduce metal to metal interaction and wear. Reducing friction in piston skirts, valve springs and bearings extends their life and lowers the engines overall friction coefficient. This again translates into more power at the crankshaft instead of negative parasitic power losses. Dry films also assist during break-in periods, less wear means less metal residue in the oil pan, etc., etc., etc. As dry film and friction reducing lubricants are bonded into the metal, under extreme conditions and duress, they remain in and on the parts long after grease or oils have burned away.
-Don Redmon
The following is a brief and general customer’s guide to Thermal Coatings. Thermal and friction reducing applications are applied after the part is etched. The part is cleaned, the coating is applied and then oven cured. This insures that the application, unlike paint, is tougher and more than skin deep.
The semi-gloss black external coating is a Thermal Dispersant, it gets rid of heat faster and more efficiently than bare metal, it also sheds mud and rubber. Typical applications are cylinders, cylinder heads, intake manifolds, brake calipers, radiators and oil coolers. Always properly warm up your engine before operational loading. It will now take longer for your engine to come to operating temperature. Clean with soap, water and/or light solvents, do not leave it to soak in a solvent tank.
The silvery looking Thermal Barrier coating keeps heat from passing through it. It is applied to piston crowns, combustion chambers, valve faces and exhaust pipes, to name just a few uses. This coating will raise the working temperature inside of the combustion chamber. We suggest that you start with a colder range spark plug and watch your readings, this is especially important the smaller the bore size. Clean carefully, do not scrape the surface, polish with extra fine steel wool using light pressure.
The dark gray application is a Dry Film Lubricant. It is used on piston skirts, bearings and valve springs. This is the softest of the coatings and depending on the clearances, it will visually wear. Use light compatible oil when installing a piston in a cylinder. Remember though that the applications are more than skin deep.
Depending on engine modifications, your location, air pressure and quality, etc., you may need to re-adjust or re-jet your engines fuel and ignition systems. Do this carefully, i.e. richer and retarded is better to start with. Always err on the side of caution, it is much less costly. Please do not hesitate to call with any questions you may have.
Hello, my name is Don Redmon and I am the owner of Replika Maschinen, Inc. We are an airflow, porting, engine and thermal coating facility located in the Santa Cruz, California area. I have been professionally involved in the racing, high performance and technical automotive and motorcycle markets for over a quarter of a century.
I was recently honored when asked to write a column for "Speedoptions.com". This column will cover a wide variety of technical subjects and I welcome your comments and suggestions for possible future columns. If there is something of a technical nature you would like to know more about, let us know. In the meantime you can expect to see future articles on:Engine blueprinting, what it is and why I should care.Cylinder heads, competition valve jobs, various stages of porting, and types of porting.Thermal coatings, cryogenics, various types of dynamometers and what the differences are.Turbochargers, superchargers, nitrous oxide, where these devices come from and what we should be doing with them.We will also talk about camshafts and the largely ignored valve spring. I will get into basic subjects such as gasolines, octane's and both pump and racing fuels and why you should care. What the differences are between gasoline, methanol and nitro methane. Multi valved and multi camed cylinder heads, fuel injection, how new is this technology really, and where it comes from.
But most of all, this column will be about information. There are many products and services out their vying for your hard earned dollars. Some products and services are good choices while others are less than good or less than optimum for what you are trying to accomplish. Only when primed with some basic knowledge and hopefully the spark to seek out additional information, can you then venture forth, as a better-informed and more questioning consumer. Therefore, our first topic will be about selecting symbiotic and workable combinations, a continually overlooked but very important aspect of engine building. As we are an air flow/ porting facility, we deal with many different types of internal combustion engines and racing disciplines. Two strokes for motocross and road racing, four strokes, high output and high revving automotive and motorcycles, Imports to big cubic inch Domestic V-8's. We even work with low revving, very high torque, large capacity diesel engines improving power and fuel efficiency. However, no matter what we are doing or whom we are working with we hear the same story again and again, a story every shop in existence has heard and experienced frequently. It goes like this: The consumer calls or comes in with a box of different parts all by different manufactures. The customer then proceeds to ask to have this menagerie assembled into an engine that will propel his vehicle into the 6-second zone.
Marketing in this country is an art form. If you doubt this, consider the pet rock, or grass growing plaster gargoyles and professional wrestling. We are the world leaders in marketing and packaging of products. My point here is that just because something looks good, comes in a great package and promises you straight teeth and a better sex life, it does not mean that it is what you need in your particular car or that it will work with your particular engine combination. Engines, like people, are made up of various component parts. These parts must work in harmony in order to receive the greatest return from the effort put into them. The better the parts work together, the greater the harmony, the greater the output of power. Trying the throwing mud at the wall and then seeing what sticks approach to component selection is not a wise path to follow. So before you buy, formulate a plan of action as to what you want to sensibly achieve and what you can afford to achieve. Then, contact the companies and shops you would like to be working with on your project and ask their advice. Contact others and get their advice, read about your engine, go to the races and ask questions. Then, with your engine builder's help, make sensible realistic decisions and purchases. Always purchase quality components. Remember you get what you pay for.
At Replika Maschinen, inc. our primary business is improving airflow and volumetric efficiency primarily via porting of the engines air passageways. However, we also seek to improve volumetric efficacy by improving the quality of the air or fluid charge by lowering the temperature of that charge to gain more oxygen per volume. Air is the working fluid of internal combustion engines, so air is the fluid I am referring to here. When we lower the temperature of our working fluid/air, it becomes more dense. One of the ways in which we lower the temperature of the inlet charge and engine and achieve this volumetric advantage is through the world of THERMAL COATINGS. Around the end of the Second World War the need to go higher, further, faster enveloped the defense and aeronautical industries. These desires spawned a metallurgical revolution in exotic materials. But along with these exotic materials for air frames and more powerful engines came new problems of protection. Corrosion resistance, noise suppression, friction reducers, thermal barriers and thermal dispersants were invented or modified to address these new concerns. The automotive racing industry discovered these substances sometime in the 1970's. However, as they soon learned, racecars and their engines are not jet-propelled aircraft and vice-versa. Coatings that worked just perfectly in the sustained and controlled environment of aerospace often meet its match in an automobile engine. Zirconia based ceramics for example, have very different expansion rates, 4.16x10-6, when compared to aluminum alloy at 13.7x10-6 over temperature ranges of 80 to 800 deg. F. Fortunately there were individuals who saw the benefits and worked hard to develop coatings specifically for the automotive industry. These are what we here at Replika Maschinen, inc. and other facilities around the world use and are what we will concern ourselves with as the topic of conversation to follow.
Turbo Compressor Housing
But first, what are thermal coatings and what do they do? Thermal coatings come in two basic categories; thermal dispersants to help get rid of heat and thermal barriers to block heat. Thermal dispersants help the coated part shed heat faster than that part normally would dispense with were it bare or un-coated. Thermal dispersants are generally exterior coatings and therefore primarily work via convection, but conduction is also involved. Convection is the transfer of heat by the laminar or turbulent motion of a liquid or a gas from one region of space to another. The convection style transference of heat as it relates to the automotive type world would include radiators, oil-coolers, brake calipers, rotor carriers and hubs, exhaust systems, turbocharger/supercharger housings and air and liquid cooled engines. Conduction is the transfer of thermal energy through a material or between two bodies in contact. This would apply to heat transfer between cylinder and cylinder head or any two or more parts in contact with one another. So for our pop quiz, which theory of thermal heat transference covers lap dancing.
Miata 1.6 Cylinder Head
THERMAL DISPERSANTS as the name implies, reduce or remove excessive heat. As mentioned earlier, a large majority of an engines potential heat energy ends up as waste. An engine must dispense with this excessive heat or else burn up. Coated cylinder heads dispose of excessive heat at a far greater rate then un-coated heads. Reducing the onset of engine killing detonation, lower intake charge temperatures and less chance of blowing head gaskets due to cylinder head warpage and walk are just a few more advantages. Engines work on heat but this heat must be properly dealt with. Too little and the engine will not operate in an efficient manner, too much and it will melt down. In early 1998, the INDY LITES organization decided to conduct a test of their then current oil cooler and thermal dispersants. They had the oil cooler thermal dispersant coated, it was then tested on and off the track. They experienced a 15% reduction in oil temperatures; the smaller older coated oil cooler out performed its newer and larger replacement. All INDY LITES teams now run coated oil coolers. In NASCAR, Bill Elliot and many others, run coated radiators to help reduce internal engine and engine bay temperatures and improve aerodynamics via smaller radiator openings. Brake parts and systems can also be coated. Obviously the faster heat is dissipated the less likely the chance of fade or out rite failure. As a side benefit, coated parts shed dirt and rubber and are far less likely to plug up, as readily as un-coated parts will. In our next article, we will discuss Thermal Dispersants and Dry Film Lubricants. Thanks, until next time, Don Redmon, Replika Maschinen, inc.
Stop Making Sense Thermal Coatings Part II Article by: Don Redmon (Friday, May 18, 2001) (522 reads)
Extra High Temperature Thermal Barrier Coated Expansion Chamber In part 2 of our article on thermal coatings, we will discuss Thermal Barriers and Dry Film Lubricants. Thermal barriers as the name implies are barriers or shields to thermal events or heat. An internal combustion engine is basically a thermally controlled air pump. So various engine events will depend on heat to function properly while others depend on the elimination of heat to live. Remember, an engine's working fluid is air, introduce an air charge into the combustion chamber, provide an ignition source with a combustible compound to heat it at the correct time, and you produce work. Sounds easy, however heat is the key to making a little power, a lot of power, or seizing the engine. Heat as it relates to a high performance racing engine is different conceptually from what is wanted by a smog controlled street engine. While the conceptual differences are there, as are the reasons for each argument, the results are similar. Combustion efficiency produces more work with less fuel and less residual emissions. Areas to hold heat into include, the combustion chamber and exhaust systems and areas to shed heat include most everything else. On the intake side, the cooler the intake air the more dense the air charge. However, there are instances, EPA, CARB environmental controls, evaporation levels of certain fuels, that demand higher but moderated temperatures. Controlling the heat of the combustion process and the exhaust elimination system can assist in maintaining control over both engine interior and exterior temperatures. An engine certainly does get hot under the hood. Studies have documented temperature drops of 100 to 300 degrees of under hood heat. What do you think dropping under hood temperature 100 degrees does to your inlet charge temperatures? Barrier coatings on exhaust system components contain the heat into the system and preclude the heat from just migrating around the semi-closed container called your engine bay. By controlling this engine heat, we put it to work for us in the area of power increases instead of simply an ambulatory road kill grill. I am sure you have all heard the term ceramics applied to automotive-coated parts. While ceramics are used in automotive applications, their use is still relatively new and cutting edge. In the "1980's" I remember magazine articles and talk about an "Oval Track" style "Midget" engine, designed, built and run using ceramics and plastics in place of steel and aluminum for internal engine parts. Ferrari and other Formula One teams are currently using ceramics in both engine and suspension applications. But for the average guy or gal on the street, their use is minimal outside of thermal barriers. Barrier coatings do contain amounts of ceramic but they are not pure ceramic for one very important reason, coefficient of expansion. Aluminum alloy for example, will expand at 13.7x 10(-6th) while zirconia based ceramics expand at 4.16x 10(-6th) in the temperature realms of 80 to 800 degrees Fahrenheit. Aluminum obviously expands at a far greater rate than does the ceramic, which makes it hard to keep them in contact with each other for very long. While steel headers for example, will expand less than aluminum, steel is still affected by heat more than and therefore its expansion rate is greater than the ceramic too. Coating pistons, valves, combustion chambers, turbocharger exhaust manifolds and turbine housings, exhaust ports, and exhaust headers and pipes is where thermal barrier coatings most useful work is done. Keeping the combustion heat into the combustion chamber where it belongs and not allowing it to migrate throughout the engine is important. As exhaust gas speed and wave intensity is directly related to temperature elevation and the consistency of the temperature throughout the length of the pipe. Maintaining elevated and constant temperature throughout the length of the system is paramount to effective scavenging and evacuation. Thermal barriers hold that heat into the system helping it to perform better and also protecting the coated parts from rust corrosion and premature damage. So where does all of that internally combusted heat go to? It goes to the same places it normally does but now we are trying to control and positively use the normally wasted heat energy. Normally, part will go into the cooling system to be eliminated via the radiator or in the case of air-cooled engines, cooling fins. Part will go out the exhaust system as additional waste. The remaining thirty percent or less is actually used to produce work and turn the crankshaft. It should not take a rocket scientist to realize that increasing the latter's percentage even in small amounts will garner additional returns in work and power. Here at Replika Maschinen, inc., we have found that coated pistons will stave off the damaging effects of uncontrolled excessive combustion chamber heat, detonation and/or pre-ignition. This could ordinarily lead to a hole in the piston in two strokes and/or ring land damage in a four-stroke engine. Thermal barrier coated pistons transfer less heat to wrist pins, cage bearings and the general crankcase area. Thermal barrier coated intake and exhaust valves will not transfer their normal amount of heat directly to the valve springs, hence the springs last far longer than normal. As the valves themselves do not get as hot, they do not wear the respective valve seat contact areas as quickly, parts last longer with less heat. Thermal barriers will not totally prevent engine damage caused by tuning errors that lead to severe detonation and or pre-ignition. They will not improve your sex life, eliminate problems caused by general ignorance and/or help from your friends who know everything or create world peace. However, they will protect vital internal engine components far longer and provide an extended range of extra protection when things do go wrong. By coating these parts, we hold the heat in to where it belongs, the combustion chamber. We gain usage of more of the potential and available BTU's (British Thermal Units a system of measuring heat potential) to use in order to convert our inlet charge to work. Heating the air to turn the crankshaft translates into the potential for more work and power. Dry Film Lubricants and friction reducers are lubricants that maintain themselves in a dry state. Friction is a force that resists motion between two bodies or parts in contact with one another. Lubrication is necessary to reduce friction and prevent metal to metal contact within your engine's various moving parts. A thin film of oil, sometimes only ". 000025 of an inch" thick is all that holds your engine parts apart and moving. Dry films work and provide protection at all times, however, they provide special lubricity and extra protection when combined with liquid lubricants. You might think of dry film lubricants, as you would think of freeze dried foods, you add liquid to make them work even better. Dry films are a mix of various very slick materials, in a resin-bonded matrix. The application process is similar to thermal coatings and the lubricants are imbedded into the metal. Dry film lubricants are designed to reduce friction, which produces heat. They also reduce metal to metal interaction and wear. Reducing friction in piston skirts, valve springs and bearings extends their life and lowers the engines overall friction coefficient. This again translates into more power at the crankshaft instead of negative parasitic power losses. Dry films also assist during break-in periods, less wear means less metal residue in the oil pan, etc., etc., etc. As dry film and friction reducing lubricants are bonded into the metal, under extreme conditions and duress, they remain in and on the parts long after grease or oils have burned away.
First Posting to engine blog
Welcome to Engineblog.
The purpose of this site is to encourage questions, responses and extended education about Ceramic Coatings used in High Performance Automotive and general internal combustion applications.
Feel free to get into any discussion you see here.
In addition to this blog I'll respond personally to your questions about ceramic coatings.
Stan Wilder
www.engineceramics.com
The purpose of this site is to encourage questions, responses and extended education about Ceramic Coatings used in High Performance Automotive and general internal combustion applications.
Feel free to get into any discussion you see here.
In addition to this blog I'll respond personally to your questions about ceramic coatings.
Stan Wilder
www.engineceramics.com
Subscribe to:
Posts (Atom)
Your Comments are welcome.
Feel free to add your comments to the individual postings.
Your comments are subject to review by the moderator.
Cycle and Automotive Coatings
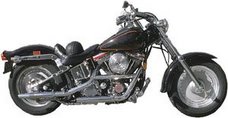
Blog Archive
-
▼
2007
(28)
-
▼
June
(28)
- lowering the underhood temps
- How can I ceramic coat the inside of my headers?
- Doing it the hard way ..... and how!
- Porsche ceramic exhaust
- Pictures and albums about Ceramic headers publishe...
- Johannesburg - June 2005
- Black Satin Results
- Performance Report
- TEST REPORT We just received a repo...
- PLASMA VS LIQUID COATINGS
- 10% increase
- Corvette Fever
- Precision Engine Magazine
- Speedway Illistrated Discussion
- Dyno Test
- Coating Valve Springs
- Coating Valve Train Components
- Coating the Oil Pan
- Coating Pistons
- Coating Cylinder Heads
- Coating Headers and Exhaust Manifolds
- Coating a Crankshaft
- Coating Engine Bearings
- Coating a Valve
- Coating an Intake Manifold
- Spray -On Horsepower, Ceramic Coatings
- Thermal Coatings by Don Redmon
- First Posting to engine blog
-
▼
June
(28)